Black POM plastic sheet, also known as acetal or polyoxymethylene (POM), is a versatile engineering plastic that offers high strength, stiffness, wear resistance and chemical resistance. It is widely used in various industries for making precision parts that require low friction, high rigidity and excellent dimensional stability. But how does black POM plastic sheet compare with other common engineering plastics? In this article, we will compare black POM plastic sheet with ABS, PET, PBT and PA plastics in terms of their properties and applications, and explain why black POM plastic sheet is a superior choice for many products.
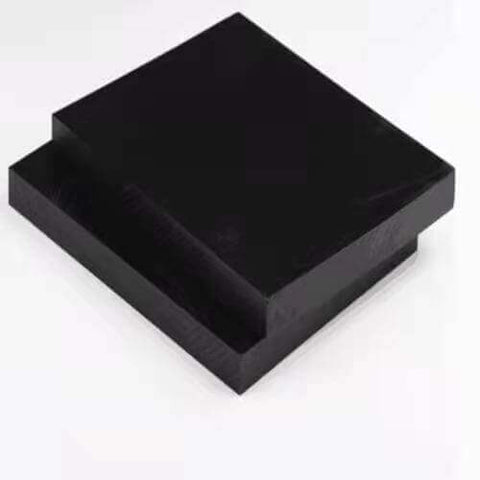
ABS Plastic
ABS (acrylonitrile-butadiene-styrene) plastic is a popular thermoplastic that combines the strength and rigidity of acrylonitrile and styrene with the toughness and impact resistance of butadiene rubber. ABS plastic has good formability, transparency and bonding properties, and can be easily molded into various shapes and sizes. ABS plastic is widely used for making housings, enclosures, toys, appliances and consumer electronics.
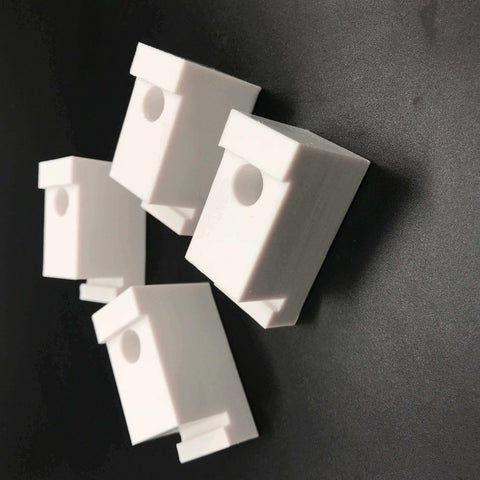
However, ABS plastic also has some disadvantages compared to black POM plastic sheet. ABS plastic has poor chemical resistance and is prone to stress cracking when exposed to dilute acids, alkalis, fuels, oils and solvents. ABS plastic also has poor fatigue resistance and tends to degrade under repeated stress cycles. ABS plastic has lower mechanical strength and wear resistance than black POM plastic sheet, especially in damp or dry environments. ABS plastic also has lower thermal stability and UV resistance than black POM plastic sheet, and can fade or crack when exposed to sunlight or high temperatures.
Therefore, black POM plastic sheet is a better choice than ABS plastic for applications that require high strength, wear resistance, chemical resistance, thermal stability and UV protection, such as gears, bearings, valves, plugs and connectors in automotive, electrical and medical industries.
PET Plastic
PET (polyethylene terephthalate) plastic is a thermoplastic polyester that offers high strength, rigidity and hardness, good creep resistance and hydrolysis resistance up to +70°C. PET plastic has very low moisture absorption, outstanding sliding behavior and low wear, especially compared to POM plastic in both damp and dry environments. PET plastic also has good chemical resistance against acids and can withstand sterilization processes. PET plastic is widely used for making bottles, containers, films, fibers and fabrics.

However, PET plastic also has some disadvantages compared to black POM plastic sheet. PET plastic has lower impact strength than POM plastic, especially at low temperatures, which makes it more brittle and prone to cracking or shattering under impact. PET plastic also has lower thermal stability than POM plastic and can deform or melt under high temperatures or rapid temperature changes. PET plastic also has lower electrical insulation than POM plastic and can conduct electricity or cause sparks in high voltage or high frequency environments.
Therefore, black POM plastic sheet is a better choice than PET plastic for applications that require high impact strength, thermal stability and electrical insulation, such as insulators, switches, connectors and housings in electrical and medical industries.
PBT Plastic
PBT (polybutylene terephthalate) plastic is a thermoplastic polyester that is characterized by high strength, rigidity, dimensional stability and thermal deformation resistance. It has a low tendency to creep and has very good friction and wear properties. PBT plastic also has better impact strength than PET plastic, especially at low temperatures, which makes it easier to modify with fibers. PBT plastic has excellent resistance to chlorine and caustic cleaning solutions, making it the perfect choice for food industry applications. It also offers very good electrical characteristics, very low moisture absorption and has a very low coefficient of thermal expansion. PBT plastic is widely used for making electrical components, connectors, housings, keyboards and automotive parts.
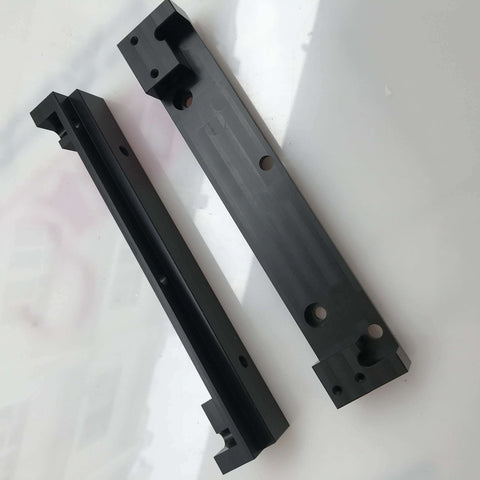
However, PBT plastic also has some disadvantages compared to black POM plastic sheet. PBT plastic has lower mechanical strength and wear resistance than POM plastic, especially in dry environments. PBT plastic also has lower chemical resistance than POM plastic and can degrade or swell when exposed to dilute acids, alkalis, fuels, oils and solvents. PBT plastic also has lower thermal stability than POM plastic and can lose its properties or discolor when exposed to high temperatures or sunlight.
Therefore, black POM plastic sheet is a better choice than PBT plastic for applications that require high strength, wear resistance, chemical resistance and thermal stability, such as gears, bearings, valves, plugs and connectors in automotive, electrical and medical industries.
PA Plastic
PA (polyamide) plastic, also known as nylon, is one of the most important and useful plastics thanks to its outstanding wear resistance, very good temperature and impact properties and good coefficient of friction. PA plastic can withstand high loads and impacts without breaking or deforming. It can also resist fatigue and creep under repeated stress cycles. PA plastic has good chemical resistance against dilute acids, alkalis and solvents. PA plastic is widely used for making friction bearings, gears, rollers, seals and housings in various machines and devices.
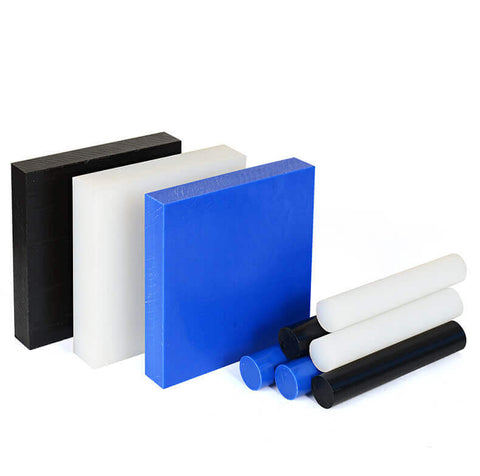
However, PA plastic also has some disadvantages compared to black POM plastic sheet. PA plastic has high moisture absorption and can swell or shrink when exposed to water or humidity. This can affect its dimensional stability and mechanical properties. PA plastic also has lower rigidity and hardness than POM plastic and can deform or bend under stress or heat. PA plastic also has lower thermal stability than POM plastic and can melt or burn when exposed to high temperatures or flames.
Therefore, black POM plastic sheet is a better choice than PA plastic for applications that require low moisture absorption, high rigidity, hardness and thermal stability, such as insulators, switches, connectors and housings in electrical and medical industries.
Conclusion
Black POM plastic sheet is a versatile engineering plastic that has many advantages over other common engineering plastics. It has high strength, stiffness, wear resistance and chemical resistance. It also has low friction, low moisture absorption, high thermal stability and UV protection. It is suitable for making various precision parts that require low friction, high rigidity and excellent dimensional stability in automotive, electrical and medical industries. If you are interested in learning more about black POM plastic sheet or other engineering plastics, please visit www.beeplastic.com for more information.
We are a professional custom plastics manufacturer with over 20 years of experience in producing various engineering plastics products according to your specifications. We have advanced equipment, skilled workers and strict quality control system to ensure the quality of our products. We also offer competitive prices, fast delivery and excellent after-sales service to meet your satisfaction.
If you want to order black POM plastic sheet or other engineering plastics products from us, please send us an email at beeplastic@beeplastic.com with your requirements. We will reply you as soon as possible with a quotation.
Thank you for reading this article.
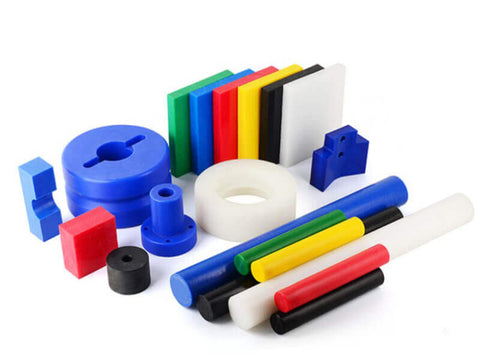