You will not be allowed to compare more than 4 products at a time
View compareCustom Plastic Solutions
Discover the properties and versatile applications of our custom plastic.
Get a Quote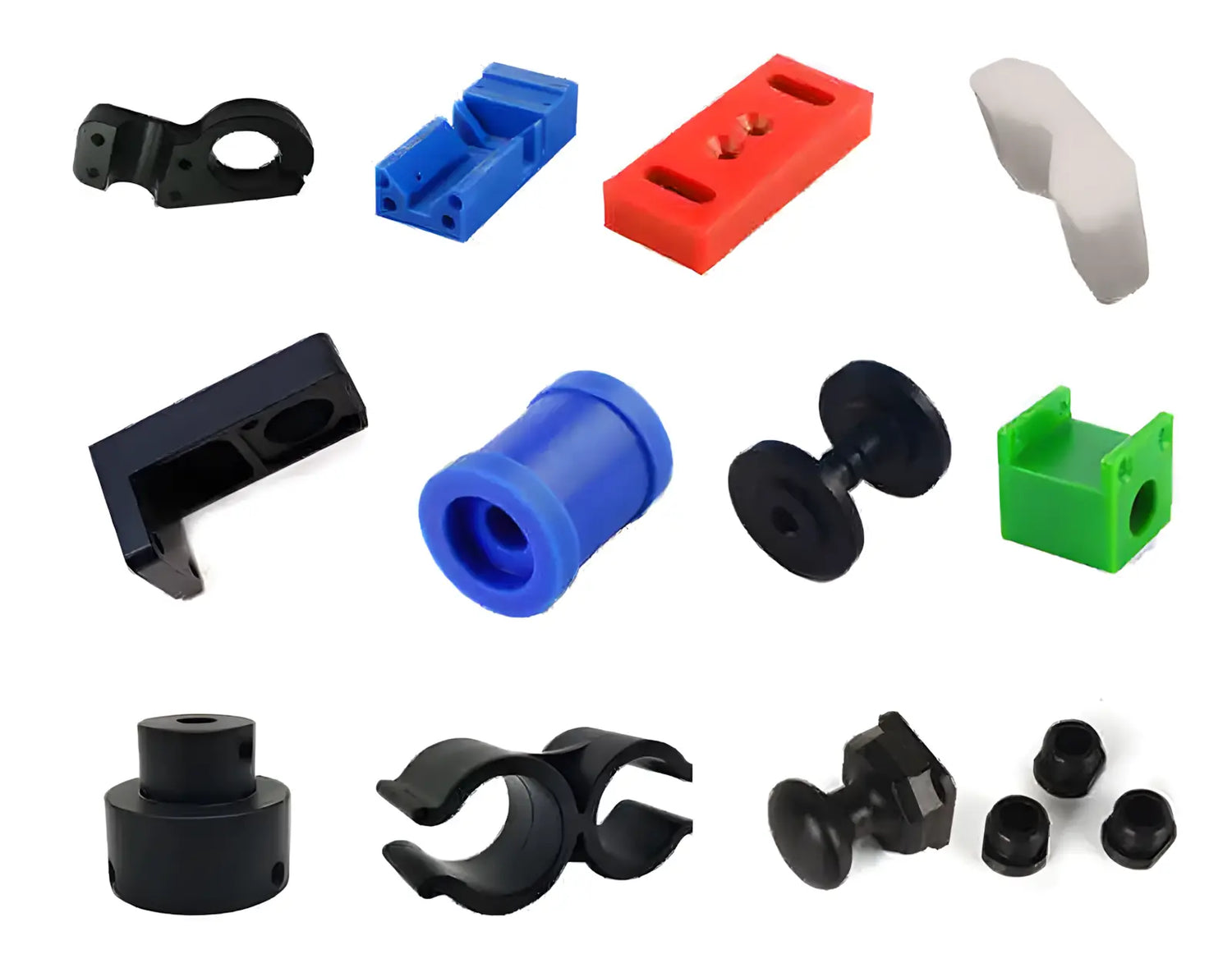
HDPE Plastic
HDPE Customization Services by Bee Plastic

Are you looking for a reliable and professional partner to handle your HDPE customization needs?
Do you want to get high-quality HDPE products that meet your specifications and requirements?
If yes, then you have come to the right place.
Bee Plastic is a leading provider of HDPE customization services. We have over 20 years of experience in working with HDPE plastic, a versatile and durable material that has many advantages and applications.
What is HDPE Plastic?
HDPE stands for high-density polyethylene, a type of polyethylene that is made from petroleum. HDPE plastic has a very high strength-to-density ratio, which means it is strong and lightweight. HDPE plastic is also resistant to chemicals, corrosion, abrasion, impact, and weathering. HDPE plastic is a thermoplastic, which means it can be melted and reshaped multiple times without losing its properties.

- High impact strength and resistance to abrasion, chemicals, and corrosion
- Low water absorption and moisture permeability
- Excellent electrical and thermal insulation
- Good flexibility and weldability
- Food-safe and recyclable
such as:
- Lightweight: HDPE has a low density compared to other plastics, which makes it easier to transport and handle.
- Stiff: HDPE has a high tensile strength and modulus, which makes it resistant to deformation and stress cracking.
- Chemical resistant: HDPE is inert to most acids, bases, solvents, oils, and greases, which makes it suitable for various industrial and environmental applications.
- Impact resistant: HDPE can withstand high impact forces without breaking or shattering, which makes it ideal for protective equipment and packaging.
- Non-leaching: HDPE does not release any harmful substances into the environment or the products it contains, which makes it safe for food and beverage storage and medical devices.
HDPE plastic is one of the most commonly used plastics in the world. It accounts for over 34% of the global plastic market. It is used for various products such as pipes, bottles, containers, cutting boards, toys, furniture, and more.
What are the Benefits of HDPE Products?
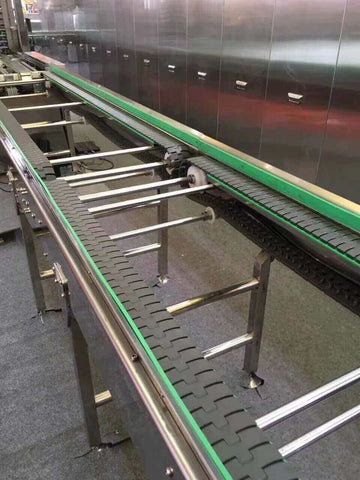
HDPE products have many benefits that make them ideal for various applications and industries. Some of the benefits are:
- High durability and longevity: HDPE products can last for decades without cracking, breaking, or degrading.
- Low maintenance and easy cleaning: HDPE products do not require painting, coating, or sealing. They are also easy to clean with soap and water or disinfectants.
- Food-safe and recyclable: HDPE products are FDA compliant and suitable for food contact applications. They are also recyclable and environmentally friendly.
- Cost-effective and versatile: HDPE products are low-cost compared to other materials such as metal or wood. They are also versatile and can be used for many purposes.
What are the Applications of HDPE Products?
HDPE products have a wide range of applications in various industries and sectors. Some of the examples are:
-
Mechanical equipment and parts: HDPE products are suitable for mechanical equipment and parts due to their high strength, low friction, and good machinability. They can be used for gears, bearings, bushings, rollers, etc. They can also be used for machine guide rails that require smooth movement and wear resistance.
- Marine and boating: HDPE products are ideal for marine and boating applications due to their resistance to saltwater, UV rays, and weathering. They can be used for boat hulls, docks, pontoons, buoys, etc.
- Commercial kitchens: HDPE products are FDA compliant and suitable for commercial kitchens due to their hygiene, ease of cleaning, and resistance to bacteria and stains. They can be used for cutting boards, countertops, sinks, etc.
- Storage: HDPE products are perfect for storage applications due to their durability, low maintenance, and resistance to chemicals and impacts. They can be used for fuel tanks, water tanks, storage sheds, bins, etc.
- Piping systems: HDPE products are excellent for piping systems due to their flexibility, leak-proofness, and resistance to corrosion and abrasion. They can be used for water supply, drainage, irrigation, gas distribution, etc.
- Furniture: HDPE products are a great alternative to wood for furniture due to their low cost, environmental friendliness, and resistance to insects and rotting. They can be used for chairs, tables, cabinets, etc.
such as:
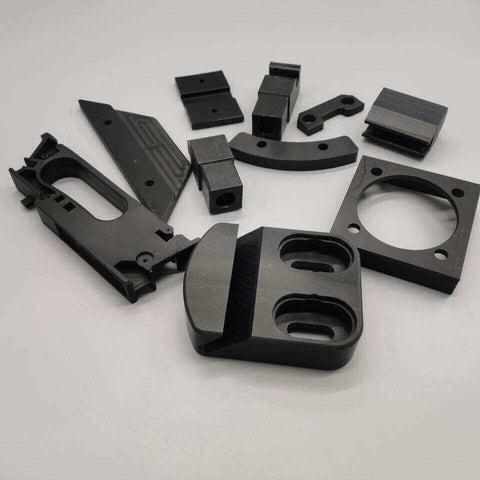
- Containers: HDPE can be used to make bottles, jars, jugs, buckets, drums, tanks, etc. for storing liquids or solids.
- Cutting boards: HDPE can be used to make cutting boards that are hygienic, easy to clean, and resistant to knife marks.
- Pump and valve parts: HDPE can be used to make pump and valve parts that are corrosion-resistant, wear-resistant, and self-lubricating.
- Washers: HDPE can be used to make washers that are flexible, resilient, and resistant to water and chemicals.
- Bearings and bushings: HDPE can be used to make bearings and bushings that are low-friction, low-noise, and low-maintenance.
- Piping and tubing: HDPE can be used to make piping and tubing that are leak-proof, flexible, and resistant to pressure and temperature changes.
- Tanks: HDPE can be used to make tanks that are strong, lightweight, and resistant to corrosion and impact.
What are HDPE Fabrication and Customization?

HDPE fabrication is the process of transforming HDPE plastic into various shapes and forms, such as sheets, rods, tubes, profiles, etc. HDPE fabrication can be done by different methods such as extrusion, injection molding, blow molding, rotational molding, etc.
HDPE customization is the process of modifying HDPE products according to the customer’s specifications and needs, such as cutting, drilling, bending, welding, etc. HDPE customization can be done by different tools such as saws, drills, routers, heat guns, welders, etc.
Bee Plastic offers both HDPE fabrication and customization services to suit your project’s requirements. We can produce HDPE products in different sizes, colors, finishes, and grades. We can also add features such as logos, labels, holes, slots, etc.
How does HDPE custom processing work and what are the different methods available?
HDPE custom processing is the process of transforming raw HDPE material into customized products that meet specific requirements and specifications. HDPE custom processing can be done using different methods, depending on the desired outcome and functionality of the product. Some of the most common methods are:
-
Thermoforming: This is a process of heating and molding HDPE sheets into various shapes using vacuum or pressure. Thermoforming can create products such as containers, trays, lids, signs, displays, etc.
- CNC milling: This is a process of cutting and carving HDPE material into precise shapes using computer-controlled machines. CNC milling can create products such as gears, valves, fittings, housings, etc.
- Injection molding: This is a process of injecting molten HDPE material into a mold cavity under high pressure. Injection molding can create products such as bottles, caps, toys, handles, etc.
- Vacuum forming: This is a process of forming HDPE sheets over a mold using vacuum suction. Vacuum forming can create products such as panels, covers, shells, etc.
- Drilling: This is a process of creating holes in HDPE material using rotating cutting tools. Drilling can create products such as pipes, tubes, rods, etc.
- Die cutting: This is a process of cutting HDPE material into various shapes using a die or a template. Die cutting can create products such as gaskets, washers, seals, etc.
- Grinding: This is a process of smoothing and polishing HDPE material using abrasive tools. Grinding can create products such as bearings, bushings, rollers, etc.
- Bending: This is a process of bending HDPE material into curved or angled shapes using heat or force. Bending can create products such as frames, brackets, hooks, etc.
- CNC turning: This is a process of rotating and shaping HDPE material using computer-controlled machines. CNC turning can create products such as shafts, spindles, screws, etc.
- Welding: This is a process of joining HDPE material using heat or pressure. Welding can create products such as tanks, ducts, fittings, etc.
What are the advantages of HDPE custom processing over standard products?
HDPE custom processing is the process of transforming raw HDPE material into customized products that meet specific requirements and specifications. HDPE custom processing can offer many advantages over standard products, such as:

- Flexibility: HDPE custom processing can create products of any shape and size, depending on your needs and specifications. Whether you need HDPE products that are flat, curved, round, square, or irregular, HDPE custom processing can make it happen. You can also choose the thickness, color, and finish of your HDPE products. HDPE custom processing gives you the freedom and flexibility to design and create products that suit your project perfectly.
- Quality: HDPE custom processing can ensure that the products have consistent dimensions, tolerances, finishes, and colors, according to the quality standards and regulations of the industry.
- Efficiency: HDPE custom processing can reduce waste and save time and money by using advanced technologies and equipment that optimize the production process.
- Innovation: HDPE custom processing can enable the creation of new and improved products that meet the changing needs and demands of the market.
Why Choose Bee Plastic for Your HDPE Customization Needs?
Bee Plastic is your trusted partner for all your HDPE customization needs. Here are some of the reasons why you should choose us:
- We have a state-of-the-art facility equipped with the latest technology and machinery for HDPE fabrication and customization.
- We have a team of skilled and experienced technicians who can handle any type of HDPE project with precision and quality.
- We have a fast turnaround time and competitive pricing for our HDPE services.
- We have a customer-oriented approach and we work closely with you to understand your needs and expectations.
- We have a reputation for excellence and satisfaction among our clients.
Contact Us Today for a Free Quote
If you are interested in our HDPE customization services, please contact us today for a free quote.
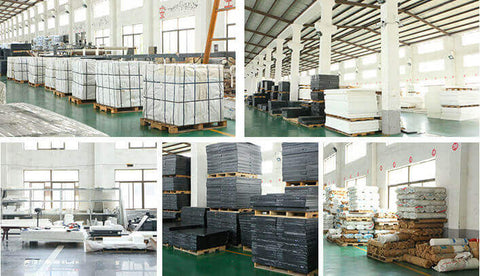
You can reach us by:
- Email: beeplastic@beeplastic.com
- Online form: Request a Quote – beeplastic
Thank you for choosing EshengPlastic as your custom acrylic fabrication partner!
We look forward to hearing from you and working with you on your HDPE customization project. Thank you for choosing Bee Plastic.😊
Explore Our Material Selection
In addition to current materials, we offer sales and processing services for a variety of materials. Click on the name of a material below to learn more about its properties and applications:
Material Name | Full Name | Applications | Properties |
---|---|---|---|
HDPE | High-Density Polyethylene | Piping, Bottles | High Strength-to-Density Ratio |
UHMW-PE | Ultra-High-Molecular-Weight Polyethylene | Conveyor Belts, Bearings | Extremely High Wear Resistance |
Nylon | Polyamide | Gears, Bearings | High Mechanical Strength, Good Wear Resistance |
PI | Polyimide | Flexible Printed Circuits | High Heat Resistance |
PEI | Polyetherimide | Medical Devices, Aircraft Interiors | High Strength, Flame Resistance |
PEEK | Polyether Ether Ketone | Aerospace Parts, Medical Implants | High Temperature and Chemical Resistance |
PP | Polypropylene | Packaging, Textiles | Chemical Resistance, Elasticity |
PET | Polyethylene Terephthalate | Beverage Bottles, Food Containers | High Strength, Thermoformability |
PAI | Polyamide-imide | Automotive Components, Electrical Insulation | High Strength, Thermal Stability |
Acrylic | Polymethyl Methacrylate (PMMA) | Displays, Lenses | Transparency, Weather Resistance |
PTFE | Polytetrafluoroethylene | Non-Stick Coatings, Gaskets | Low Friction, Chemical Resistance |
POM | Polyoxymethylene (Acetal) | Precision Parts, Gears | High Stiffness, Low Friction |
PC | Polycarbonate | Safety Glasses, CDs | High Impact Resistance, Transparency |
PPS | Polyphenylene Sulfide | Automotive Parts, Electronics | High Temperature Resistance, Chemical Stability |
PVC | Polyvinyl Chloride | Pipes, Cable Insulation | Durability, Chemical Resistance |
PVDF | Polyvinylidene Fluoride | Chemical Processing Equipment | High Chemical Resistance, Purity |
PU | Polyurethane | Foam Seating, Insulation Panels | Flexibility, Durability |
FR-4(G10) | Flame Retardant Glass-Reinforced Epoxy Laminate | Printed Circuit Boards | Flame Resistance, Mechanical Strength |
Bakelite | Phenol Formaldehyde Resin | Electrical Insulators, Radio Casings | High Mechanical Strength, Heat Resistance |
ABS | Acrylonitrile Butadiene Styrene | Automotive, Electronics, Medical Devices | Durable, Impact Resistant, Easy to Machine |
Learn More
Fully Customizable to Your Specifications
At BeePlastic, we offer precision cutting and machining to produce sheets and rods that perfectly fit your project's specific dimensions and requirements.
Tailored Solutions Across Industries
Explore Our Full Range of Plastic Materials
Discover the versatility and quality of our extensive plastic materials portfolio. From standard sheets to highly specialized rods, each product is designed to meet the diverse needs of industries including aerospace, automotive, and healthcare. Browse our collection to find the perfect material suited to your project requirements.
Browse Our Material Catalog