In the bustling world of product presentation and storage, the custom acrylic box stands out as a beacon of clarity, durability, and versatility. "Unlock the Secrets to Choosing the Perfect Custom Acrylic Box: A Purchasing Agent's Guide" is your comprehensive roadmap to navigating the intricate landscape of acrylic materials, ensuring that every purchasing agent is equipped with the knowledge to make informed decisions.

From understanding the nuances between cast and extruded acrylic to mastering the art of design considerations such as size, thickness, and color options, this guide delves deep into the factors that make a custom acrylic box not just a container, but a statement. We'll walk you through the manufacturing process, shedding light on the customization capabilities that can transform a simple box into a bespoke masterpiece tailored to your project's specific needs.
Budgeting is often a tightrope walk, but with our cost analysis, you'll learn how to navigate the financial aspects of custom acrylic box procurement, uncovering cost-saving strategies without compromising on quality. Quality assurance is paramount, and we provide insights into ensuring your boxes meet the highest standards, ready to elevate your project from ordinary to extraordinary.
Dive into our case studies where real-world applications bring the versatility and impact of custom acrylic boxes to life, from retail displays that captivate shoppers to museum exhibits that protect and showcase history's treasures.
"Unlock the Secrets to Choosing the Perfect Custom Acrylic Box: A Purchasing Agent's Guide" is more than just a blog post; it's a treasure trove of industry insights, practical advice, and inspirational examples designed to empower purchasing agents with the confidence to select the ideal custom acrylic boxes for their unique projects. Join us on this journey to unlock the full potential of your projects with the perfect acrylic solution.
Understanding Custom Acrylic Box Materials
When it comes to selecting the perfect custom acrylic box for your project, the choice of material plays a pivotal role. Acrylic, known for its durability and clarity, offers a versatile solution for a myriad of applications. However, not all acrylic is created equal, and understanding the differences between the types available is crucial for making an informed decision.
The Basics of Acrylic
Acrylic, a synthetic polymer of methyl methacrylate, is renowned for its glass-like clarity and strength. It's a popular choice for custom boxes due to its lightweight nature and resistance to impact, making it superior to glass in many applications. The material's inherent UV resistance and ability to be fabricated and molded into various shapes and sizes further enhance its appeal for custom projects.
Types of Acrylic for Custom Boxes
The two primary types of acrylic used in custom box fabrication are cast acrylic and extruded acrylic.
-
Cast Acrylic: Known for its excellent optical clarity and uniform thickness, cast acrylic is produced by pouring liquid acrylic into molds. This method results in a material that is stronger and more scratch-resistant, making it ideal for high-quality custom acrylic boxes where aesthetic appeal and durability are paramount. Cast acrylic is also more suitable for projects requiring complex shapes or detailed engraving.
-
Extruded Acrylic: Produced by pushing acrylic pellets through a highly controlled, heated extruder, extruded acrylic offers a more cost-effective solution with greater dimensional stability. While it may not match the superior strength or scratch resistance of cast acrylic, it provides a consistent thickness and is easier to cut and shape, making it a good choice for larger production runs or applications where budget constraints are a consideration.
Choosing the Right Acrylic Material
Selecting between cast and extruded acrylic hinges on the specific requirements of your project. Consider factors such as:
- Durability: If your custom box will be subjected to frequent handling, transportation, or harsh environmental conditions, cast acrylic's superior strength and scratch resistance might be necessary.
- Clarity: For projects where optical clarity is non-negotiable, such as display cases for high-value items, cast acrylic is the preferred choice.
- Budget: If cost is a major concern, extruded acrylic offers a more budget-friendly option without significantly compromising on quality.
- Complexity of Design: The flexibility and ease of shaping extruded acrylic make it suitable for projects with intricate designs or those requiring precise dimensional tolerances.
Understanding the unique properties and benefits of each type of acrylic material allows you to make a choice that aligns with your project's needs, ensuring that your custom acrylic box not only meets but exceeds expectations. Whether you prioritize durability, clarity, cost, or design complexity, there's an acrylic solution that fits the bill, providing a perfect blend of form and function for your custom project.
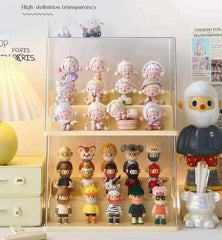
Design Considerations for Custom Acrylic Boxes
When crafting the perfect custom acrylic box, every detail counts. Purchasing agents have the unique challenge of balancing aesthetic appeal with practical functionality. By focusing on key design elements such as thickness, color, and size, you can ensure your custom acrylic boxes not only meet but exceed project requirements.
Optimizing Thickness for Durability and Aesthetics
The thickness of the acrylic plays a crucial role in the overall durability and appearance of the box. Thicker acrylic offers enhanced strength and is ideal for larger boxes or those expected to support heavier items. However, it's essential to strike a balance; overly thick acrylic can detract from the box's visual appeal, making it appear bulky.
For display purposes, where the emphasis is on clarity and lightness, a thinner acrylic may be preferable. It maintains the box's protective qualities while ensuring the contents remain the focal point. Consider the end use of the box—will it be purely decorative, or does it need to withstand regular handling? Answering this question will guide you in selecting the optimal thickness.
Choosing the Right Color and Transparency
Color and transparency are more than just aesthetic choices; they influence the viewer's interaction with the box's contents. Clear acrylic is the go-to for showcasing items without obstruction, making it perfect for museum displays, retail cases, or any setting where visibility is key.
However, colored acrylic can be used strategically to enhance or contrast the items inside. For instance, a black acrylic base can make lighter objects stand out, while frosted acrylic offers a subtle veil that can intrigue viewers, encouraging closer inspection. When selecting colors, consider the ambiance of the space where the box will be placed and how the color will complement or contrast with its surroundings.
Sizing Custom Acrylic Boxes to Fit
Size is perhaps the most straightforward yet critical design consideration. The dimensions of your custom acrylic box should be tailored not just to the size of the items it will house but also to the space where it will be displayed. A box that's too large can overwhelm its contents, while one that's too small may not adequately protect or display the items inside.
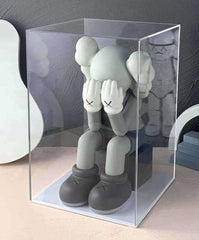
Accurate measurements are essential. Allow for sufficient clearance around the items, considering any padding or mounts that may be needed. Additionally, think about how the box will integrate into its intended environment—will it need to fit within specific shelving, on a countertop, or alongside other displays?
Navigating Design Complexity
The design process for custom acrylic boxes involves a delicate balance between form and function. By carefully considering thickness, color, and size, purchasing agents can create custom solutions that not only protect and showcase their contents but also enhance the overall design aesthetic of the space they occupy. Remember, each design element should be chosen with the project's specific goals in mind, ensuring a custom acrylic box that perfectly aligns with both practical needs and visual aspirations.
The Manufacturing Process of Custom Acrylic Boxes
The journey from concept to completion for custom acrylic boxes is a fascinating blend of art and science. This process not only transforms a simple piece of acrylic into a functional and aesthetic product but also offers a wide range of customization options to meet specific project requirements. Understanding the steps involved can help purchasing agents make informed decisions and collaborate more effectively with manufacturers.
Initial Design Phase
The manufacturing process begins with the initial design phase, where the vision for the custom acrylic box takes shape. This stage involves detailed discussions between the client and the manufacturer to outline the box's purpose, dimensions, thickness, color, and any special features such as locks, hinges, or UV protection. Advanced software is often used to create precise 3D models of the box, allowing for virtual visualization and adjustments before physical production starts. This digital blueprint is crucial for ensuring that the final product will meet the client's expectations.
Material Selection
Choosing the right acrylic material is the next critical step. As discussed earlier, the choice between cast and extruded acrylic will depend on the box's intended use, desired aesthetic, and budget constraints. The selected acrylic sheets are then prepared for production, ensuring they are of the highest quality and free from defects.
Cutting and Shaping
With the design and materials finalized, the acrylic sheets are cut to size using high-precision tools such as laser cutters or CNC (Computer Numerical Control) machines. These technologies allow for incredibly accurate cuts and intricate shapes, essential for custom designs. The edges of the cut pieces can be polished to achieve a clear, glass-like finish, enhancing the box's overall appearance.
Assembly and Customization
The individual pieces of the box are then assembled. This can involve bonding techniques using special acrylic adhesives that create strong, seamless joints, ensuring the box's integrity and durability. It's at this stage that customization options truly come to life. Features like engraving, printing, or embedding LED lights are added according to the client's specifications. These custom touches can transform a standard acrylic box into a unique piece that perfectly fits its intended purpose and environment.
Quality Control and Final Inspection
Before the custom acrylic box is deemed ready for delivery, it undergoes a rigorous quality control process. This includes inspecting the box for any defects in material or craftsmanship, ensuring that all dimensions are accurate, and verifying that any custom features have been correctly implemented. Only after passing this final inspection will the box be packaged and shipped to the client.
Emphasizing Customization Options
The manufacturing process of custom acrylic boxes is highly adaptable, allowing for a vast array of customization options. Whether it's a specific color palette, intricate designs cut into the box, or functional features tailored to the contents it will hold, the possibilities are nearly limitless. This flexibility makes custom acrylic boxes an excellent choice for a wide range of applications, from retail displays and museum exhibits to protective casings and personal collectible showcases.
Understanding the detailed process behind the creation of custom acrylic boxes highlights the craftsmanship and customization that go into each piece. For purchasing agents, this knowledge ensures that they can guide their projects to success, achieving a perfect balance between form, function, and budget.
Cost Analysis of Custom Acrylic Boxes
Navigating the financial aspects of procuring custom acrylic boxes requires a keen understanding of the various cost components involved. A detailed cost analysis not only helps in budgeting effectively but also in identifying opportunities for cost savings without compromising on quality. Let's break down the primary factors contributing to the cost and explore strategies for managing your budget efficiently.
Material Costs
The choice of material is a significant cost driver in the production of custom acrylic boxes. As we've discussed, cast acrylic tends to be more expensive than extruded acrylic due to its superior clarity, strength, and versatility in customization. The thickness of the acrylic also plays a crucial role; thicker materials will naturally increase the cost. Deciding on the right type and thickness of acrylic based on the specific needs of your project is essential for controlling costs.
Design and Customization Costs
The complexity of the design significantly impacts the overall cost. Simple designs with standard dimensions and minimal customization are more cost-effective to produce. In contrast, intricate designs requiring precise cuts, complex shapes, or additional features such as engraving, printing, or embedded LED lighting will increase production costs. Working closely with your manufacturer to simplify designs without sacrificing the essential features can help manage these costs.
Manufacturing and Labor Costs
The manufacturing process involves several steps, each requiring skilled labor, from the initial design phase to cutting, shaping, assembly, and finishing. The labor cost is influenced by the complexity of the project and the precision required in the manufacturing process. Opting for designs that are easier to produce and require less manual labor can contribute to cost savings.
Quantity and Scale
The quantity of custom acrylic boxes ordered can also affect the cost per unit. Larger orders often benefit from economies of scale, reducing the cost per box. If possible, planning your needs in advance and ordering in bulk can lead to significant savings. However, it's important to balance the benefits of bulk ordering with the risk of overproduction and excess inventory.
Budgeting and Cost-Saving Strategies
- Prioritize Essential Features: Identify which features of the custom acrylic box are essential and which are nice-to-have. Focus your budget on the must-haves to ensure functionality and aesthetics without overspending.
- Opt for Simpler Designs: Whenever possible, choose simpler designs that meet your needs. This can significantly reduce both material and labor costs.
- Material Selection: Consider the pros and cons of cast vs. extruded acrylic for your project. Opting for extruded acrylic when high strength and clarity are not critical can offer substantial savings.
- Bulk Ordering: If you have a recurring need for custom acrylic boxes, ordering in larger quantities can leverage economies of scale, reducing the cost per unit.
- Collaborate with Manufacturers: Early collaboration with your manufacturer can reveal additional ways to optimize the design for cost-efficiency without compromising quality.
Understanding the factors that contribute to the cost of custom acrylic boxes and employing strategic budgeting and cost-saving measures can significantly impact the overall expense of your project. By carefully considering each aspect of the design and production process, purchasing agents can achieve a balance between quality, functionality, and cost, ensuring the successful completion of their projects within budget.
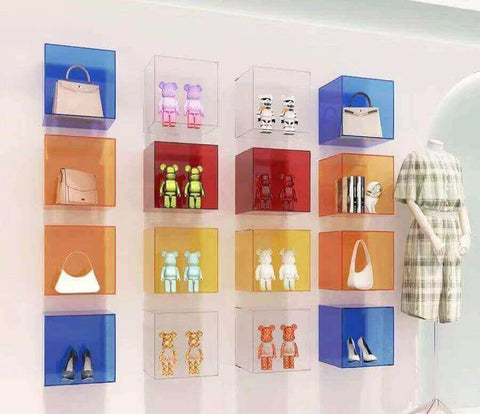
Quality Assurance for Custom Acrylic Boxes
In the realm of custom acrylic boxes, the assurance of quality is not just a phase in the manufacturing process; it's a comprehensive approach that ensures the final product not only meets but exceeds the expectations of clients. Quality control (QC) plays a pivotal role in every step, from material selection to the final inspection before delivery. Let's delve into the importance of QC and how to ensure that your custom acrylic boxes adhere to the highest standards of quality.
The Role of Quality Control in Acrylic Box Manufacturing
Quality control in the manufacturing of custom acrylic boxes is crucial for several reasons. It prevents defects, ensures durability, and maintains the aesthetic integrity of the box. A rigorous QC process helps in identifying and rectifying issues early in the manufacturing process, saving time and resources by avoiding costly reworks or replacements. Moreover, consistent quality assurance practices contribute to building trust and reliability with clients, establishing a reputation for excellence in the market.
Material Quality and Inspection
The journey of quality assurance begins with the material selection. Using high-grade acrylic is essential for the longevity and visual appeal of the box. Upon receipt of the acrylic sheets, a thorough inspection for any defects such as scratches, bubbles, or inconsistencies in thickness is conducted. This initial step ensures that only the best materials are used in the production of the boxes.
Precision in Cutting and Assembly
As the acrylic sheets move to the cutting and shaping phase, precision is key. Modern manufacturing techniques, such as laser cutting and CNC machining, offer high accuracy but still require regular calibration and monitoring to maintain their precision. The assembly process, involving bonding and joining the acrylic pieces, demands meticulous attention to detail. The adhesive application must be controlled to avoid air bubbles or misalignment, ensuring seamless joints and clear edges.
Customization and Finishing Touches
Custom features and finishing touches, such as engraving, polishing, or adding hardware, are where the custom acrylic boxes truly come to life. Each of these processes requires its own set of quality checks. For instance, engraving depth and clarity are inspected to match the design specifications, while polishing is checked for a smooth, flawless finish. These details contribute significantly to the overall quality and appearance of the final product.
Final Inspection and Quality Certification
Before the custom acrylic boxes are packaged and shipped, a comprehensive final inspection is conducted. This includes a detailed review of dimensions, design conformity, strength, and aesthetics. Any deviations from the client's specifications are addressed at this stage. Providing a quality certification or a report detailing the QC measures undertaken throughout the manufacturing process can offer additional assurance to clients about the quality of their custom acrylic boxes.
Ensuring Quality Standards
To ensure that the final product meets your standards, it's important to:
- Communicate Clearly: Provide detailed specifications and expectations to the manufacturer from the outset.
- Choose Reputable Manufacturers: Partner with manufacturers known for their commitment to quality and who have robust QC processes in place.
- Request Samples: If possible, ask for samples or prototypes to assess the quality and craftsmanship before proceeding with the full order.
- Stay Involved: Regular updates and checkpoints throughout the manufacturing process can help catch any potential issues early.
Quality assurance for custom acrylic boxes is a critical component that safeguards the product's integrity, functionality, and aesthetic appeal. By prioritizing QC at every stage of the manufacturing process, purchasing agents can confidently deliver custom acrylic boxes that stand the test of time and continue to delight clients with their precision and beauty.
Case Studies: Successful Projects with Custom Acrylic Boxes
The versatility and durability of custom acrylic boxes have made them a popular choice across various industries, from retail to museum exhibitions. These real-world case studies highlight the innovative use of acrylic boxes, the challenges encountered, and the creative solutions that ensured the success of each project.
Case Study 1: Retail Display Innovation
Challenge: A high-end electronics retailer sought to create a dynamic display for their latest smartphone model. The primary challenge was to design a display box that was both secure and interactive, allowing customers to view the product from all angles without compromising on security.
Solution: The solution was a series of custom acrylic boxes with a clear, durable design, incorporating a locking mechanism that was both subtle and effective. The boxes were mounted on a rotating base, enabling 360-degree viewing. LED lighting was embedded within the acrylic, highlighting the smartphone's features. The use of cast acrylic ensured maximum clarity and durability, while the custom design met the retailer's specific security needs.
Case Study 2: Museum Exhibit Preservation
Challenge: A museum planned an exhibit featuring rare, fragile artifacts that required protection from environmental factors and potential damage while on display. The challenge was to create a display solution that offered maximum visibility without compromising the artifacts' preservation.
Solution: Custom acrylic boxes were designed with UV-filtering acrylic to protect the artifacts from light damage. The boxes were also sealed to create a controlled environment, preventing dust and humidity from affecting the artifacts. Each box was custom-sized to fit individual pieces, with minimalistic stands that did not detract from the artifacts themselves. This approach allowed visitors to appreciate the artifacts up close in a safe and controlled manner.
Case Study 3: High-Value Product Launches
Challenge: For the launch of a luxury watch collection, the brand wanted a display solution that mirrored the sophistication and value of their products. The challenge was to design a display box that was both elegant and secure, enhancing the presentation of each watch.
Solution: The solution involved creating sleek, custom acrylic boxes with high-gloss black bases and clear tops. The design included a secure locking mechanism hidden within the base, maintaining the display's aesthetic appeal. Each box featured custom-cut foam inserts that cradled the watches, providing stability and a luxurious backdrop. Integrated LED lighting subtly illuminated the watches, drawing attention to their features and craftsmanship.
Lessons Learned and Solutions Found
These case studies demonstrate the flexibility of custom acrylic boxes in meeting specific project requirements. Key takeaways include:
- Customization is Key: Tailoring the design to meet the unique needs of each project ensures both functionality and aesthetic appeal.
- Material Matters: Choosing the right type of acrylic can significantly impact the project's success, from UV-filtering options for artifact preservation to high-gloss finishes for luxury displays.
- Innovative Features Enhance Functionality: Incorporating features like LED lighting or custom inserts can elevate the presentation and functionality of the acrylic boxes.
Through creative design and careful material selection, custom acrylic boxes can solve complex display and preservation challenges, proving their value in a wide range of applications.
In navigating the intricacies of custom acrylic boxes, from the initial selection of materials to the final touches of quality assurance, it's clear that these versatile creations offer more than just a protective enclosure; they provide a canvas for innovation and aesthetic expression. Whether it's enhancing retail displays, preserving priceless artifacts, or launching luxury products, custom acrylic boxes stand at the intersection of functionality and elegance. By understanding the critical factors involved in their design, manufacturing, and implementation, purchasing agents can unlock the full potential of acrylic boxes to elevate their projects. The case studies highlighted serve as a testament to the transformative power of well-crafted custom acrylic solutions, proving that with the right approach, the possibilities are as clear and boundless as the material itself.
Ready to transform your project with the perfect custom acrylic box? Don't let this opportunity slip through your fingers! Scroll down now and fill out the contact form at the bottom of the page. Let's make your vision a reality together!