In the blog post "Transforming Industrial Equipment: How PPS CNC Machining is Changing the Game," we delve into the revolutionary world of PPS (Polyphenylene Sulfide) material and its transformative impact on industrial equipment manufacturing. The post begins by exploring the unique properties of PPS, emphasizing its high temperature resistance, chemical stability, and mechanical strength — key factors that make it an ideal choice for CNC machining in industrial applications.
🎉🎉🎉Limited Time Offer Use code: QR4GNY08SHVR at checkout and enjoy a special discount on your entire order! 👉PPS board

We then shift our focus to the latest innovations in PPS CNC machining techniques, highlighting how these advancements are not only enhancing precision but also driving efficiency and cost-effectiveness in the production of industrial machinery parts. This section is particularly insightful for those keen on understanding the cutting-edge technology shaping today's industrial landscape.
The heart of the post features compelling case studies that demonstrate the successful application of PPS CNC machined parts in various industries. These real-world examples provide a tangible look at how PPS components have improved the functionality and durability of industrial machinery, offering a persuasive argument for their adoption.
A critical comparative analysis follows, where PPS CNC machining is pitted against traditional manufacturing methods. This comparison sheds light on the numerous benefits of PPS CNC machining, including reduced production time, enhanced precision, minimized waste, and overall cost savings.
Finally, we gaze into the future, speculating on the evolving role of PPS CNC machining in industrial equipment. This section is designed to give readers a glimpse into what lies ahead, discussing potential technological advancements and emerging industrial needs that could further shape the landscape of equipment manufacturing and modification.
This comprehensive post is a must-read for anyone in the industrial sector looking to stay abreast of the latest trends and innovations in equipment manufacturing, particularly those involving the game-changing capabilities of PPS CNC machining.
Understanding PPS Material and Its Advantages in CNC Machining
When it comes to industrial equipment manufacturing, the choice of material plays a pivotal role in determining the efficiency, durability, and overall performance of the produced parts. One such material that stands out in the realm of CNC machining is Polyphenylene Sulfide (PPS). This high-performance thermoplastic polymer offers a unique combination of properties that make it an excellent choice for a wide range of industrial applications.
Key Properties of PPS
High Temperature Resistance
One of the most notable features of PPS is its high temperature resistance. PPS can withstand prolonged exposure to high temperatures without losing its structural integrity. This makes it an ideal material for components that are subjected to extreme heat during operation, such as parts in automotive engines or industrial machinery.
Chemical Stability
Chemical stability is another hallmark of PPS. This material exhibits remarkable resistance to a wide array of chemicals, including acids, alkalis, and organic solvents. This property is particularly beneficial in industries where equipment is regularly exposed to harsh chemical environments, ensuring longevity and reliability of the components.
Mechanical Strength
The mechanical strength of PPS is yet another reason for its widespread use in CNC machining. PPS parts are known for their rigidity, dimensional stability, and high strength-to-weight ratio. These characteristics are crucial in applications where parts must endure heavy loads or mechanical stress, ensuring that the equipment functions smoothly under demanding conditions.
Why PPS is an Excellent Choice for Industrial Equipment
The combination of high temperature resistance, chemical stability, and mechanical strength makes PPS an outstanding material for industrial equipment. Its ability to maintain performance under harsh conditions translates into longer-lasting parts, reduced maintenance costs, and increased overall efficiency of machinery. Furthermore, the adaptability of PPS to precision CNC machining processes allows for the creation of complex and intricate parts with tight tolerances, essential for many industrial applications.
In conclusion, the selection of PPS for CNC machining in industrial equipment manufacturing is a strategic choice that offers numerous benefits. Its superior properties ensure that machinery operates reliably and efficiently, even in the most challenging environments. As industries continue to evolve and demand more from their equipment, materials like PPS will play an increasingly important role in meeting these advanced requirements.
Innovations in PPS CNC Machining Techniques
The world of CNC machining is constantly evolving, with new technologies and techniques emerging regularly. These advancements are particularly significant when it comes to machining Polyphenylene Sulfide (PPS), a material highly valued in industrial applications for its robust properties. Let's delve into the latest innovations in CNC machining specifically tailored for PPS, and how they contribute to more precise, efficient, and cost-effective production of industrial equipment parts.
Advanced Precision in PPS Machining
Enhanced Accuracy with Modern CNC Equipment
One of the most significant advancements in PPS CNC machining is the leap in accuracy and precision offered by modern CNC equipment. These state-of-the-art machines can handle complex geometries and intricate designs with unprecedented precision. This is crucial for industries where even the slightest deviation can lead to significant operational issues.
Improved Surface Finishing Techniques
Another area of innovation is in surface finishing. New techniques in CNC machining have enabled smoother and more consistent finishes on PPS parts. This improvement not only enhances the aesthetic appeal but also contributes to the functionality, especially in parts where surface smoothness affects performance.
Efficiency and Cost-Effectiveness in PPS Machining
Streamlined Production Processes
Advancements in CNC machining technology have streamlined the production process for PPS parts. Automated tooling and programming capabilities allow for quicker setup times and faster machining speeds. This efficiency reduces the time from design to production, ultimately leading to cost savings for manufacturers.
Reduction in Material Waste
Modern CNC machines are designed to be more material-efficient. With advanced software, these machines can optimize cutting paths and tool usage, significantly reducing material waste. This is not only cost-effective but also aligns with sustainable manufacturing practices, an increasingly important consideration in industrial production.
The Future of PPS CNC Machining
Looking ahead, the ongoing innovations in CNC machining for PPS point to a future where even more complex and high-performance parts can be produced with greater efficiency and lower costs. As technology continues to advance, we can expect to see further improvements in precision, speed, and sustainability in PPS machining processes.
In conclusion, the innovations in PPS CNC machining are transforming the production of industrial equipment parts. These advancements are making it possible to produce parts that are more precise, efficient, and cost-effective, meeting the ever-growing demands of various industries. As we continue to embrace these technological developments, the potential for PPS in industrial applications seems boundless.
Case Studies: Successful Industrial Applications of PPS CNC Machined Parts
The practical applications of PPS (Polyphenylene Sulfide) CNC machined parts in various industries serve as powerful testimonials to their effectiveness. In this section, we explore real-world case studies from sectors like automotive, aerospace, and general manufacturing, showcasing how PPS CNC machined components have significantly enhanced the functionality, durability, and efficiency of industrial machinery.
Automotive Industry: Revolutionizing Component Durability
High-Performance Engine Parts
In the automotive sector, PPS CNC machined parts have been instrumental in producing high-performance engine components. For instance, a leading automotive manufacturer replaced traditional metal parts with PPS components in their engine design. The result was a remarkable improvement in heat resistance and chemical stability, leading to longer-lasting engines with reduced maintenance needs.
Lightweight and Efficient Designs
Another case study in the automotive industry highlights the use of PPS in creating lightweight yet durable parts. By integrating PPS components, manufacturers have been able to reduce the overall weight of vehicles, contributing to enhanced fuel efficiency and lower carbon emissions, aligning with the industry's move towards sustainability.

Aerospace Industry: Enhancing Safety and Performance
Critical Aerospace Components
In the aerospace industry, the stakes are incredibly high when it comes to the quality and reliability of components. PPS CNC machined parts have been used in critical applications such as valve components and insulation materials. Their ability to withstand extreme temperatures and pressures has been crucial in ensuring the safety and performance of aerospace equipment.
Cost-Effective Manufacturing Solutions
One notable example involves a leading aerospace company that adopted PPS components for various interior and exterior parts of their aircraft. The switch to PPS not only provided the necessary strength and durability but also proved to be more cost-effective compared to traditional materials, without compromising on safety or quality.

Manufacturing Industry: Improving Efficiency and Longevity
Durable Machinery Components
In the broader manufacturing sector, PPS CNC machined parts have been a game-changer in enhancing the longevity of machinery. For example, a manufacturing plant reported a significant increase in the lifespan of their equipment after replacing certain metal parts with PPS components. The inherent strength and wear resistance of PPS contributed to less frequent breakdowns and lower maintenance costs.
Customized Solutions for Complex Applications
Another success story comes from a manufacturer specializing in high-precision tools. By utilizing PPS CNC machining, they were able to produce customized parts that met exact specifications, resulting in improved efficiency and precision in their operations.
In conclusion, these case studies across various industries demonstrate the transformative impact of PPS CNC machined parts. Their ability to improve functionality, enhance durability, and boost efficiency makes them an invaluable asset in the industrial world. As we continue to witness the evolution of manufacturing technologies, the role of PPS in industrial applications is poised to grow even further.
Comparative Analysis: PPS CNC Machining vs. Traditional Methods
In the realm of industrial manufacturing, the choice of production methods significantly impacts the final product's quality, efficiency, and cost. This comparative analysis focuses on PPS CNC Machining versus traditional manufacturing methods, examining key aspects such as production time, precision, waste reduction, and overall cost-effectiveness.
Production Time: Speed and Efficiency
Traditional Methods: Time-Intensive Processes
Traditional manufacturing methods, while proven, often involve time-intensive processes. For instance, manual machining and molding techniques require longer setup times and slower production rates. This can lead to extended production cycles, especially for complex parts or large orders.
PPS CNC Machining: Accelerated Production
In contrast, PPS CNC Machining significantly accelerates production time. Advanced CNC machines can rapidly produce complex parts with minimal setup time. This efficiency is particularly beneficial for large-scale production runs, where time savings translate directly into increased productivity and faster time-to-market.
Precision and Accuracy
Traditional Methods: Variability in Quality
With traditional manufacturing, achieving consistent precision can be challenging, especially for intricate designs. Manual processes are prone to human error, leading to variability in the final product's quality.
PPS CNC Machining: Unmatched Precision
PPS CNC Machining stands out for its unparalleled precision. CNC machines are capable of producing parts with extremely tight tolerances, ensuring consistent quality across all produced items. This precision is crucial in industries where even minor discrepancies can have significant implications, such as in aerospace or medical device manufacturing.

Waste Reduction: Sustainable Practices
Traditional Methods: Higher Material Waste
Traditional manufacturing methods often result in higher levels of material waste. Excess material from processes like cutting, drilling, or milling is not always recyclable or reusable, leading to inefficiencies and increased costs.
PPS CNC Machining: Minimizing Waste
PPS CNC Machining is more efficient in terms of material usage. Advanced software allows for precise calculations and optimizations, significantly reducing waste. This not only lowers material costs but also aligns with sustainable manufacturing practices, an increasingly important consideration in today's industry.
Overall Cost-Effectiveness
Traditional Methods: Cumulative Costs
While traditional methods may have lower initial investment costs, they often incur higher cumulative costs over time. Factors like longer production times, higher waste, and the need for skilled labor can add up, making these methods less cost-effective in the long run.
PPS CNC Machining: Long-Term Cost Savings
PPS CNC Machining, though it may require a higher initial investment, offers significant long-term cost savings. The efficiency, precision, and reduced waste lead to lower operational costs. Additionally, the durability and quality of PPS CNC machined parts can reduce the need for frequent replacements or repairs, further contributing to cost savings.
In conclusion, when comparing PPS CNC Machining with traditional manufacturing methods, it becomes clear that CNC machining offers significant advantages in terms of production time, precision, waste reduction, and overall cost-effectiveness. These factors make PPS CNC Machining a superior choice for a wide range of industrial applications, promising higher quality, efficiency, and sustainability.
Future Trends: The Evolving Role of PPS CNC Machining in Industrial Equipment
As we look towards the future, the role of PPS CNC Machining in industrial equipment manufacturing is poised for significant evolution. This section explores potential trends and developments in the field, considering technological advancements and emerging industrial needs that are likely to shape the future landscape of equipment manufacturing and modification.
Technological Advancements in CNC Machining
Integration of AI and Machine Learning
One of the most exciting prospects in PPS CNC machining is the integration of Artificial Intelligence (AI) and Machine Learning (ML). These technologies promise to further enhance precision, efficiency, and customization in machining processes. AI algorithms can optimize machining parameters in real-time, adapting to varying material properties and design requirements, leading to improved outcomes and reduced waste.
Advancements in 3D Printing and Additive Manufacturing
3D printing and additive manufacturing technologies are also expected to intersect more significantly with CNC machining. This integration could revolutionize how PPS parts are produced, allowing for more complex geometries and reducing the time from design to production. The combination of additive manufacturing for complex shapes and CNC machining for precision finishing could be a game-changer in the industry.
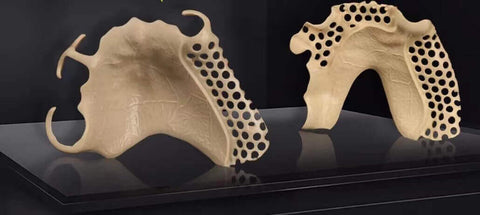
Emerging Industrial Needs
Demand for More Sustainable Manufacturing Practices
Sustainability is becoming increasingly important in industrial manufacturing. The future of PPS CNC machining will likely involve more eco-friendly practices, including the use of recycled materials and further reduction of waste. This shift not only addresses environmental concerns but also responds to the growing demand for sustainable practices from consumers and regulatory bodies.
Customization and Rapid Prototyping
As industries continue to evolve, there is a growing need for customization and rapid prototyping. PPS CNC machining is well-positioned to meet these needs, offering the flexibility to produce bespoke parts quickly and efficiently. This capability is particularly valuable in sectors like aerospace, automotive, and medical devices, where tailored solutions are often required.
Shaping the Future of Equipment Manufacturing
Collaborative Robotics and Automation
The future of PPS CNC machining will likely see increased use of collaborative robotics and automation. These technologies can work alongside human operators to enhance productivity and safety. The integration of robotics in CNC machining processes could lead to more consistent output and the ability to maintain high production rates around the clock.
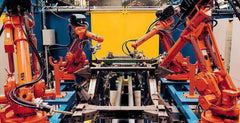
Enhanced Material Properties
Ongoing research and development in material science are expected to enhance the properties of PPS, making it even more suitable for a wider range of applications. Improvements in temperature resistance, strength, and chemical stability could open new doors for PPS in sectors where these properties are critical.
In conclusion, the future of PPS CNC Machining in industrial equipment manufacturing is bright and full of potential. With advancements in technology and a responsive approach to emerging industrial needs, PPS CNC machining is set to play a pivotal role in shaping the future of equipment manufacturing and modification. This evolution promises not only greater efficiency and precision but also a commitment to sustainability and innovation in the industrial sector.
Embracing the Future of PPS CNC Machining in Industrial Equipment
As we reach the end of our exploration into the dynamic world of PPS CNC Machining, it's clear that this technology is not just a current asset but a beacon for the future of industrial equipment manufacturing. The journey through the unique properties of PPS, the latest innovations in CNC machining techniques, impactful real-world applications, a comparative analysis with traditional methods, and a glimpse into future trends, all point to a singular truth: PPS CNC Machining is a game-changer.
The versatility and robustness of PPS, combined with the precision and efficiency of CNC machining, create a synergy that is transforming industries. From automotive to aerospace, from manufacturing to bespoke applications, the impact is profound and far-reaching. As technology continues to advance, we can expect PPS CNC Machining to not only adapt but lead the way in addressing new challenges and seizing opportunities.
For industrial manufacturers, embracing PPS CNC Machining is not just about keeping pace with current trends; it's about being at the forefront of innovation. It's about investing in a technology that promises not only enhanced performance and efficiency but also a commitment to sustainability and future growth.
As we look to the future, one thing is certain: the role of PPS CNC Machining in industrial equipment will continue to evolve, innovate, and inspire. For those ready to embrace these changes, the possibilities are as limitless as the potential of PPS itself. Let's step forward into this exciting future together, harnessing the power of PPS CNC Machining to redefine what's possible in industrial equipment manufacturing.
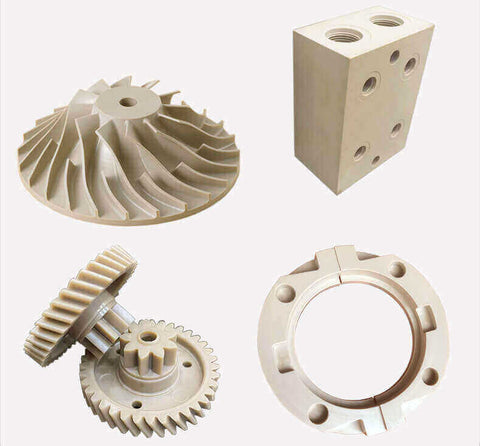
Start Transforming Your Industrial Equipment Today!
Embrace the future of manufacturing with precision and efficiency. Contact us now to explore how our PPS CNC Machining solutions can revolutionize your industrial equipment. Don’t wait – the future of advanced manufacturing is here!
🎉🎉🎉Limited Time Offer Use code: QR4GNY08SHVR at checkout and enjoy a special discount on your entire order! 👉PPS board