The Ultimate Guide to ABS Plastic Sheets for Automotive Applications
Are you looking to understand why ABS plastic sheets are a top choice in the automotive industry? This comprehensive guide covers everything you need to know about ABS sheets, from their properties and advantages to their common uses in vehicles. Discover how ABS plastic outperforms other materials in automotive manufacturing and explore the various manufacturing processes that make it a versatile choice. Learn about the benefits of using ABS plastic sheets for lightweight automotive design and how they contribute to fuel efficiency and performance. Stay updated with the latest innovative applications of ABS in modern automotive design, and understand the environmental impact and sustainability efforts surrounding this essential material. Whether you're a manufacturer or a DIY enthusiast, this guide is your go-to resource for all things ABS plastic sheets in the automotive world.
🎉🎉🎉Limited Time Offer Use code: QR4GNY08SHVR at checkout and enjoy a special discount on your entire order! 👉 ABS plastic
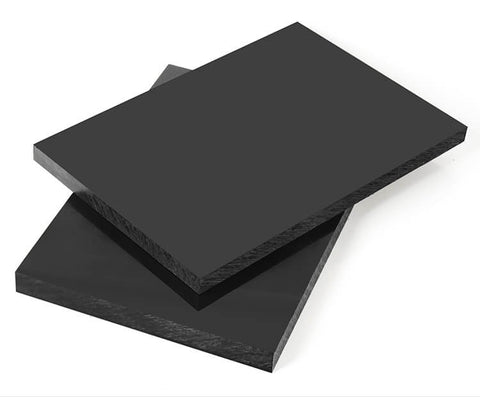
Properties of ABS Plastic Sheets and Their Advantages for Automotive Applications
Impact Resistance
ABS plastic sheets are renowned for their high impact resistance, making them a preferred choice for automotive applications. The inclusion of butadiene in the polymer structure enhances toughness, enabling ABS to absorb and dissipate energy efficiently upon impact. This property is critical for components like bumpers and side panels, which must endure collisions without cracking. The ability to withstand significant force helps protect both the vehicle and its occupants, ensuring greater safety in the event of an accident.
Lightweight
One of the standout features of ABS plastic sheets is their lightweight nature. Compared to traditional materials like metals, ABS significantly reduces the overall weight of automotive components. This reduction in weight leads to improved fuel efficiency and vehicle performance, as lighter vehicles require less energy to operate. Furthermore, the ease of handling and installation of lighter parts can reduce manufacturing costs and time, making ABS an economically attractive option for automotive manufacturers.
Heat Resistance
ABS plastic exhibits excellent heat resistance, allowing it to maintain structural integrity even at elevated temperatures. The high melting point, typically ranging from 200 to 250 degrees Celsius, makes it suitable for components exposed to heat, such as under-the-hood parts. This property is attributed to the acrylonitrile component, which provides thermal stability and prevents deformation under heat stress. The ability to withstand high temperatures without losing shape or mechanical properties ensures durability and reliability in demanding environments.
Durability
Durability is another key advantage of ABS plastic sheets. They exhibit high tensile strength and stiffness, allowing them to resist breakage under load. Additionally, ABS has excellent resistance to chemicals and environmental factors like UV exposure and moisture, making it ideal for both interior and exterior automotive applications. This durability ensures that components made from ABS can withstand the rigors of daily use and harsh conditions, maintaining their performance and appearance over time.
Versatility in Applications
The versatility of ABS plastic sheets is evident in their wide range of applications within the automotive industry. From dashboards and interior trim to wheel covers and body panels, ABS can be molded into complex shapes, providing flexibility in design and functionality. This versatility extends to its compatibility with various manufacturing processes, including injection molding, extrusion, and thermoforming, making it a versatile and cost-effective material for automotive manufacturers.
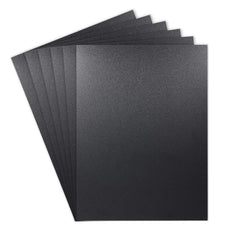
Common Uses of ABS Plastic Sheets in the Automotive Industry
Dashboards
Dashboards made from ABS plastic sheets offer excellent durability and impact resistance, making them ideal for the automotive interior. The material's high tensile strength ensures that dashboards can withstand daily wear and tear, including exposure to sunlight and temperature fluctuations. Additionally, ABS's ability to be easily molded into complex shapes allows for the integration of various design elements and functionalities, such as air vents, instrument clusters, and touchscreens. The smooth surface finish of ABS also provides an attractive and aesthetically pleasing appearance, enhancing the overall interior look of the vehicle.
Wheel Covers
ABS plastic is a popular choice for wheel covers due to its lightweight and impact-resistant properties. Wheel covers need to be strong enough to protect the wheels from debris and minor impacts while being lightweight to avoid adding unnecessary weight to the vehicle. ABS meets these requirements perfectly, offering a balance between strength and weight. Furthermore, ABS can be easily colored and finished to provide a glossy, attractive look that complements the vehicle's overall design. This versatility makes ABS a preferred material for manufacturing durable and stylish wheel covers.
Body Panels
Body panels made from ABS plastic sheets are increasingly being used in the automotive industry due to their lightweight nature and durability. Unlike metal panels, ABS panels do not corrode, providing a longer lifespan and reduced maintenance costs. The material's flexibility allows it to absorb impacts without denting, maintaining the vehicle's appearance even after minor collisions. Additionally, the ease of manufacturing ABS panels using injection molding and thermoforming processes enables the production of complex shapes and designs, offering greater design freedom for automakers.
Under-Hood Components
Under-hood components made from ABS plastic benefit from the material's heat resistance and chemical resistance. ABS can withstand temperatures up to 180°F, making it suitable for parts that are exposed to the engine's heat. Components such as battery covers, fuse boxes, and air intake systems are often made from ABS due to its ability to retain structural integrity under high temperatures. The material's resistance to chemicals like oils and coolants further enhances its suitability for under-hood applications, ensuring long-lasting performance in a demanding environment.
Interior Trim
Interior trim components made from ABS plastic sheets offer a combination of aesthetic appeal and functional benefits. The material's smooth finish allows for easy painting and customization, enabling the creation of visually appealing interior elements. ABS is also resistant to scratches and scuffs, maintaining the trim's appearance over time. Additionally, the lightweight nature of ABS contributes to the overall reduction of the vehicle's weight, enhancing fuel efficiency and performance. Common interior trim applications include door panels, center consoles, and seat backs.
By utilizing ABS plastic sheets for these various applications, automakers can take advantage of the material's unique properties to enhance the performance, durability, and aesthetic appeal of their vehicles. The versatility and cost-effectiveness of ABS make it an ideal choice for both interior and exterior automotive components.
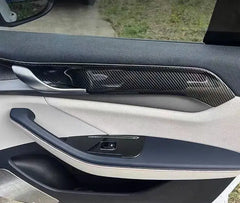
Comparison: ABS Plastic Sheets vs. Other Materials in Automotive Manufacturing
Cost
ABS plastic sheets are often chosen for automotive applications due to their cost-effectiveness. Compared to polycarbonate and nylon, ABS is generally less expensive to produce and purchase. The lower production costs are attributed to the simpler manufacturing processes and the availability of raw materials. Polypropylene, while also affordable, does not offer the same balance of properties as ABS. ABS provides a more cost-effective solution for applications requiring a combination of strength, impact resistance, and aesthetic finish.
Durability
When it comes to durability, ABS plastic exhibits excellent impact resistance and toughness. This makes it a suitable material for components that must endure significant stress and wear. Polycarbonate is known for its superior impact resistance and high tensile strength, making it ideal for applications where maximum durability is required. However, polycarbonate is more expensive than ABS. Nylon also offers high durability and excellent resistance to abrasion and wear, but it is prone to moisture absorption, which can affect its mechanical properties over time. Polypropylene, while durable, lacks the high impact resistance and surface finish quality that ABS provides.
Suitability for Different Automotive Parts
ABS plastic sheets are highly versatile and can be used for various automotive components:
-
Dashboards and Interior Trim: ABS is preferred for dashboards and interior trim due to its excellent surface finish, ease of molding, and resistance to wear and scratches. It can be easily colored and textured, enhancing the vehicle's interior aesthetics.
-
Wheel Covers and Body Panels: For wheel covers and body panels, ABS's impact resistance and lightweight properties make it an ideal choice. It provides sufficient protection against debris and minor impacts while maintaining a glossy, attractive appearance.
-
Under-Hood Components: ABS is suitable for under-hood components due to its moderate heat resistance and chemical resistance. However, for applications requiring higher temperature stability, nylon or polycarbonate might be more appropriate, despite their higher costs.
Comparison with Polypropylene
Polypropylene is lightweight and cost-effective but lacks the impact resistance and surface finish quality of ABS. It is often used in applications where high flexibility and chemical resistance are more critical than aesthetic properties, such as battery cases and chemical tanks. However, for parts that require a balance of durability, aesthetic appeal, and moderate cost, ABS is usually preferred.
Comparison with Nylon
Nylon offers excellent mechanical properties, including high tensile strength and abrasion resistance. It is used in applications that require high durability and resistance to wear, such as gears and bushings. However, nylon's tendency to absorb moisture can lead to changes in dimensions and mechanical properties, making it less suitable for certain automotive applications compared to ABS.
Comparison with Polycarbonate
Polycarbonate is known for its exceptional impact strength and clarity, making it ideal for windows, light covers, and other applications requiring transparency and high durability. However, the higher cost of polycarbonate makes ABS a more economical choice for parts where extreme durability and transparency are not critical requirements.
By comparing these materials, it becomes evident that ABS plastic sheets offer a unique balance of cost, durability, and versatility, making them a preferred choice for various automotive components. The ability to be easily molded, finished, and colored further enhances ABS's suitability for automotive applications, providing manufacturers with a cost-effective and reliable material option.
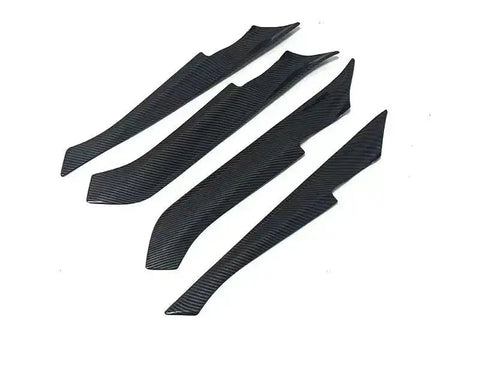
Manufacturing Processes for ABS Automotive Parts
Injection Molding
Injection molding is one of the most common methods used to manufacture ABS automotive parts. This process involves melting ABS pellets and injecting the molten plastic into a mold under high pressure. The mold shapes the plastic into the desired form as it cools and solidifies. Injection molding is particularly suitable for producing high volumes of complex parts with precise dimensions and intricate details.
- Dashboards: Injection molding allows for the creation of dashboards with integrated components such as air vents, instrument clusters, and touchscreens. The high precision of this process ensures a perfect fit and finish for these critical interior parts.
- Wheel Covers: The ability to produce large quantities of identical wheel covers makes injection molding an efficient and cost-effective choice. The resulting wheel covers are lightweight, durable, and can be easily customized with different colors and finishes.
Thermoforming
Thermoforming is another popular method used for ABS plastic sheets in the automotive industry. In this process, a sheet of ABS plastic is heated until it becomes pliable, then stretched over a mold and cooled to form the desired shape. Thermoforming is ideal for creating large, smooth-surfaced components that do not require the high precision of injection molding.
- Body Panels: Thermoforming is often used to produce body panels, such as door panels and side panels. The process allows for the efficient production of large parts with consistent thickness and surface finish. The resulting panels are lightweight and resistant to corrosion and impact.
- Interior Trim: This process is also used to manufacture interior trim components, providing a smooth, aesthetically pleasing surface that can be easily colored and textured. Thermoforming is well-suited for producing parts like door panels and center consoles that require a high-quality finish.
Extrusion
Extrusion is a process used to create continuous profiles by pushing molten ABS plastic through a shaped die. This method is typically used for producing long, uniform components such as tubes, rods, and sheets. Extrusion is highly efficient for manufacturing parts that require consistent cross-sectional shapes.
- Trim and Seals: Extruded ABS is commonly used for trim and seals in automotive applications. The consistent profile and durability of extruded ABS make it ideal for these components, which need to maintain their shape and functionality over time.
- Pipes and Fittings: The extrusion process is also used to produce pipes and fittings for various automotive systems. These components benefit from the material’s resistance to chemicals and temperature variations, ensuring reliable performance in demanding environments.
CNC Machining
CNC machining involves using computer-controlled machines to cut and shape ABS plastic sheets into precise parts. This process is highly accurate and is used for creating customized or low-volume parts that require tight tolerances and detailed features.
- Prototypes: CNC machining is ideal for producing prototypes of new automotive components. The precision of this method allows engineers to test and refine designs before mass production.
- Small Batch Parts: This process is also used for producing small batches of specialized parts that may not justify the cost of creating molds for injection molding. CNC machining ensures each part meets exact specifications and high-quality standards.
Each of these manufacturing processes leverages the unique properties of ABS plastic sheets to produce durable, reliable, and cost-effective automotive components. The choice of process depends on the specific requirements of the part, including its size, complexity, and production volume. By utilizing these versatile methods, manufacturers can meet the diverse needs of the automotive industry.
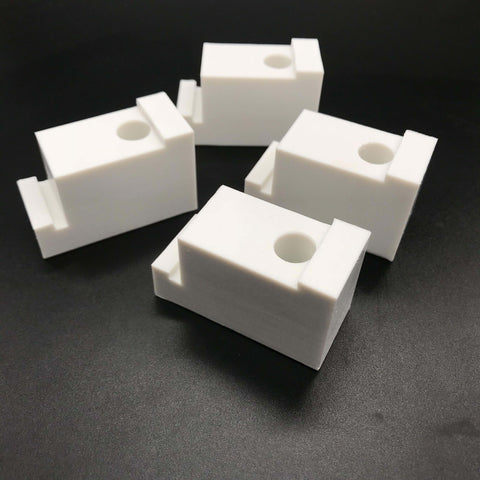
Advantages of Using ABS Plastic Sheets for Lightweight Automotive Design
Weight Reduction Benefits
The use of ABS plastic sheets in automotive design significantly contributes to weight reduction. Reducing the weight of a vehicle is one of the most effective ways to improve its fuel efficiency and overall performance. Lighter vehicles require less energy to move, which directly translates into lower fuel consumption and reduced greenhouse gas emissions. This makes ABS a valuable material in the push for more environmentally friendly and cost-effective vehicles.
Fuel Efficiency and Performance
By incorporating lightweight ABS plastic components, automakers can achieve substantial improvements in fuel economy. For every 10% reduction in vehicle weight, there is typically a 6-8% increase in fuel efficiency. This not only reduces the operational costs for consumers but also helps manufacturers meet stringent fuel economy regulations and emission standards. The lightweight nature of ABS allows for the design of components that are both durable and efficient, enhancing the vehicle's acceleration, braking, and handling characteristics.
Versatility and Design Flexibility
ABS plastic sheets offer excellent design flexibility, enabling the creation of complex and intricate automotive parts. The material's ability to be easily molded and shaped means that it can be used to produce a wide range of components, from dashboards and interior trims to body panels and wheel covers. This versatility allows designers to innovate and optimize vehicle structures without being constrained by the limitations of heavier materials like metals..
Structural Integrity and Safety
Despite its lightweight properties, ABS plastic does not compromise on structural integrity. The material is known for its high impact resistance and durability, which are crucial for automotive applications that require robust and reliable components. ABS can absorb and dissipate energy during collisions, helping to protect passengers and maintain the integrity of the vehicle's structure. This makes it an ideal choice for safety-critical parts such as bumpers and door panels.
Cost-Effectiveness
In addition to its performance benefits, ABS plastic is also cost-effective. It is generally less expensive to produce and process compared to other high-performance materials like aluminum and carbon fiber. This cost advantage, combined with its durability and ease of manufacturing, makes ABS an attractive option for automakers looking to reduce production costs while still achieving high-quality and lightweight vehicle components.
The adoption of ABS plastic sheets in the automotive industry represents a strategic move towards more sustainable, efficient, and economical vehicle design. By leveraging the unique properties of ABS, manufacturers can produce vehicles that are not only lighter and more fuel-efficient but also safer and more affordable.
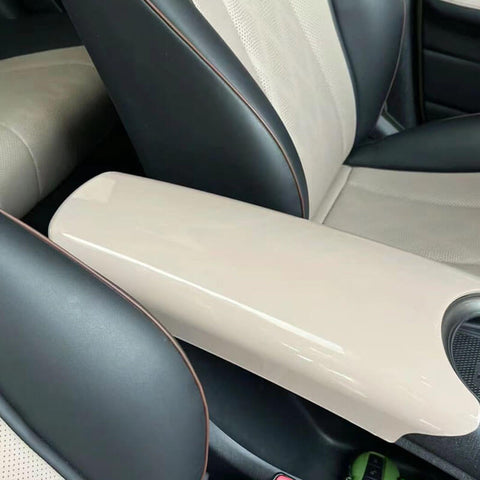
Innovative Applications of ABS Plastic Sheets in Modern Automotive Design
Custom Interior Designs
Recent innovations in ABS plastic sheets have revolutionized custom interior designs in modern vehicles. The versatility of ABS allows designers to create intricate and unique interior components that cater to the preferences of different consumers. For instance, 3D printing with ABS enables the production of highly customized dashboard panels, center consoles, and trim pieces. This technology allows for rapid prototyping and personalization, giving automakers the ability to offer bespoke interior options that enhance the driving experience.
Moreover, ABS plastic can be easily colored and textured, allowing for a wide range of finishes that can mimic leather, wood, or metal. This capability not only enhances the aesthetic appeal of the vehicle interior but also provides a durable and low-maintenance alternative to traditional materials.
Advanced Safety Features
The use of ABS plastic sheets in automotive design has also led to significant advancements in safety features. ABS is known for its high impact resistance, which makes it an ideal material for components that need to absorb and dissipate energy during a collision. Innovations in ABS formulations have further improved its impact resistance, allowing for the development of safer bumpers, door panels, and interior trims that can better protect passengers in the event of an accident.
Additionally, ABS plastic is being used to create lightweight and robust protective casings for advanced safety systems, such as airbags and electronic control units (ECUs). These casings ensure that critical safety components remain intact and functional even under extreme conditions, enhancing the overall safety of the vehicle.
Aesthetic Enhancements
Aesthetic enhancements are another area where ABS plastic sheets are making a significant impact in modern automotive design. The ability to mold ABS into complex shapes and fine details allows designers to create visually striking exterior components, such as grilles, spoilers, and mirror housings. These components not only improve the vehicle's appearance but also contribute to its aerodynamics and performance.
Moreover, the surface finish of ABS plastic can be enhanced through various techniques, including painting, metallizing, and texturing. This versatility allows manufacturers to achieve high-gloss finishes, metallic looks, and even soft-touch surfaces that add to the vehicle's visual appeal. The use of ABS plastic in aesthetic components also helps reduce the overall weight of the vehicle, contributing to better fuel efficiency and handling.
Future Trends in ABS Plastic Applications
Looking ahead, the future trends in the use of ABS plastic sheets in automotive design are focused on further improving performance, sustainability, and customization. Researchers are developing new ABS composites that incorporate recycled materials and bio-based additives to reduce the environmental impact of automotive manufacturing. These advancements aim to create more sustainable and eco-friendly ABS formulations without compromising on performance.
In addition, the integration of smart technologies into ABS components is an emerging trend. For example, embedded sensors and electronics in ABS interior trims and dashboards can provide real-time data on the vehicle's performance and environment, enhancing the overall driving experience. The continuous evolution of 3D printing technologies also promises to expand the possibilities for custom and on-demand manufacturing of ABS parts, enabling greater flexibility and efficiency in automotive production.
By leveraging these innovative applications and future trends, ABS plastic sheets continue to play a crucial role in advancing automotive design, offering a perfect balance of functionality, aesthetics, and sustainability.
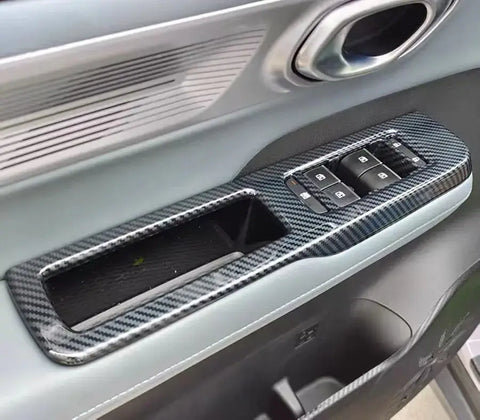
Environmental Impact and Sustainability of ABS Plastic Sheets in Automotive Applications
Recyclability of ABS Plastic
ABS plastic sheets are known for their recyclability, making them an environmentally friendly option in the automotive industry. ABS can be recycled multiple times without significant degradation in its properties, allowing for the material to be reused in various applications. This recyclability helps reduce the amount of waste sent to landfills and supports the principles of a circular economy. Municipal recycling programs increasingly accept ABS, facilitating its reuse in new automotive parts and other products.
Lifecycle Impact
The lifecycle impact of ABS plastic includes its production, use, and disposal phases. During production, ABS requires less energy compared to metals, contributing to lower greenhouse gas emissions. Its lightweight nature enhances vehicle fuel efficiency, reducing fuel consumption and emissions over the vehicle's lifespan. This makes ABS a key material in the drive towards more sustainable automotive designs.
Furthermore, the durability of ABS extends the lifespan of automotive components, decreasing the need for frequent replacements and reducing overall resource consumption. By resisting wear and maintaining structural integrity over time, ABS components help minimize the environmental impact associated with manufacturing new parts.
Bio-based and Recycled ABS
Innovations in bio-based ABS are emerging as part of the effort to enhance the sustainability of this material. Bio-based ABS incorporates renewable raw materials, reducing reliance on fossil fuels. For example, Trinseo's MAGNUM™ BIO ABS uses a combination of traditional and renewable resources, providing similar performance to conventional ABS while offering a reduced carbon footprint.
Additionally, the use of recycled ABS is gaining traction. Recycled ABS resins offer mechanical and aesthetic properties comparable to virgin ABS, making them suitable for a wide range of applications. This approach not only reduces the demand for new raw materials but also decreases the environmental impact associated with ABS production.
Steps Toward Sustainability
Several steps are being taken to improve the sustainability of ABS plastic in the automotive industry:
- Increased Recycling Programs: Expanding recycling infrastructure to ensure more ABS is collected and processed. This helps create a steady supply of recycled ABS for manufacturing new products.
- Development of Bio-based ABS: Investing in research to create ABS from renewable resources. This reduces the dependency on fossil fuels and lowers the carbon footprint of ABS production.
- Closed-loop Systems: Implementing closed-loop recycling systems within manufacturing facilities to reuse ABS scrap and waste. This minimizes material waste and supports a sustainable production cycle.
- Lightweighting Strategies: Utilizing the lightweight nature of ABS to design more fuel-efficient vehicles. Lighter vehicles consume less fuel, reducing emissions and improving environmental performance over their lifespan.
By focusing on these initiatives, the automotive industry can enhance the environmental performance of ABS plastic sheets, making them a more sustainable choice for vehicle manufacturing.
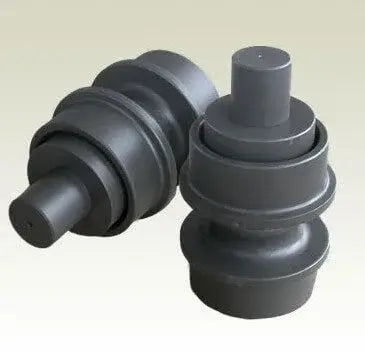
Frequently Asked Questions (FAQs) about ABS Plastic Sheets and Customization at BeePlastic
1. Can BeePlastic undertake any customization of ABS plastic sheets?
Answer: Yes, BeePlastic can handle any type of customization, including both sample customization and batch customization. We tailor our services to meet the specific needs of our customers, ensuring that each project is completed to the highest standards.
2. What file formats does BeePlastic accept for customization requests?
Answer: BeePlastic accepts a variety of file formats for customization requests, including PDF and CAD files. This flexibility ensures that our customers can provide their designs in the format that works best for them, facilitating a smooth customization process.
3. Is there a minimum order quantity (MOQ) for placing an order with BeePlastic?
Answer: No, there is no minimum order quantity (MOQ) at BeePlastic. We cater to both small and large orders, making our services accessible to a wide range of customers, from individual hobbyists to large-scale manufacturers.
4. How is the production cycle determined for customized orders?
Answer: The production cycle for customized orders at BeePlastic is determined based on the amount of orders and the complexity of the process. We communicate with our customers in real time about the production progress, ensuring transparency and timely updates throughout the manufacturing process.
5. Does BeePlastic provide samples of ABS plastic sheets, and what are the associated costs?
Answer: Yes, BeePlastic provides samples of ABS plastic sheets. The samples are free of charge, but customers are responsible for the shipping costs. This allows customers to evaluate our materials and workmanship before placing a larger order.
6. What are the key advantages of using ABS plastic sheets in automotive applications?
Answer: ABS plastic sheets are highly valued in the automotive industry for their durability, lightweight nature, impact resistance, and heat resistance. These properties make ABS ideal for components such as dashboards, wheel covers, body panels, and under-hood components, contributing to overall vehicle performance and safety.
7. How does BeePlastic ensure the quality of its customized ABS plastic sheets?
Answer: BeePlastic ensures the quality of its customized ABS plastic sheets through stringent quality control measures. Each batch undergoes thorough testing to meet industry standards and customer specifications. Our state-of-the-art manufacturing processes and experienced team ensure that every product is of the highest quality.
8. What are the environmental benefits of using ABS plastic sheets?
Answer: ABS plastic sheets are recyclable and can be reused multiple times without significant loss of properties. This reduces waste and supports sustainable manufacturing practices. Additionally, ABS's lightweight nature helps improve vehicle fuel efficiency, contributing to lower emissions and environmental impact.
9. Can BeePlastic handle large-scale production orders?
Answer: Yes, BeePlastic is equipped to handle large-scale production orders. Our advanced manufacturing facilities and scalable processes enable us to efficiently manage high-volume orders while maintaining quality and meeting delivery timelines.
10. How does BeePlastic support customers throughout the customization process?
Answer: BeePlastic provides comprehensive support to customers throughout the customization process. From initial consultation and design assistance to real-time production updates and quality assurance, we ensure a smooth and collaborative experience. Our team is always available to answer questions and address any concerns.
Conclusion
The versatility and durability of ABS plastic sheets make them an indispensable material in modern automotive design. From enhancing fuel efficiency and reducing environmental impact to enabling innovative and customizable interior and exterior components, ABS plastic sheets offer a range of benefits that support both performance and sustainability. As the automotive industry continues to evolve, embracing lightweight and recyclable materials like ABS will be crucial in meeting the demands of the future. Whether you're a manufacturer looking to improve your vehicle designs or a consumer interested in the latest advancements in automotive materials, ABS plastic sheets provide a reliable and forward-thinking solution. For more information and customized solutions, visit BeePlastic.
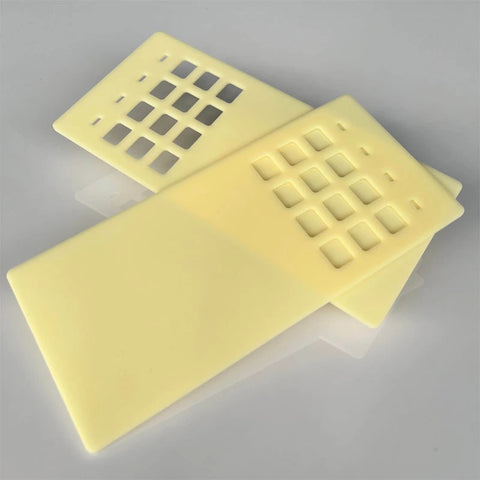
Discover Customized Solutions for Your Automotive Needs
Ready to enhance your automotive designs with durable and versatile ABS plastic sheets? Fill out our contact form below to get started with a customized solution tailored to your specific requirements. For detailed information on our ABS plastic machining services, click here.