When selecting materials for different components and parts in consumer products, engineers must balance factors like cost, durability, and manufacturing requirements. Two thermoplastics often considered are polyoxymethylene (POM) and nylon. While nylon has been a popular choice for years, POM offers some advantages that make it outperform nylon in certain applications.
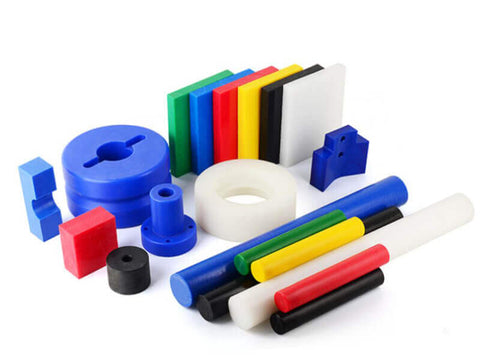
POM vs Nylon in Appliance Components
In appliances that utilize water and get washed regularly, POM can be the better material option compared to nylon. One case study looked at food processor blades - those made of nylon tended to warp and degrade over time when exposed to hot water and dishwasher cleaning cycles. POM blades maintained their shape and performance after repeated washings.
Another example is humidifier water tanks. The humidity and temperature fluctuations in these appliances contributed to cracking in nylon tanks. Switching to POM fully eliminated the cracking issue for one major manufacturer. The improved thermal and chemical resistance of POM made it outlast nylon.
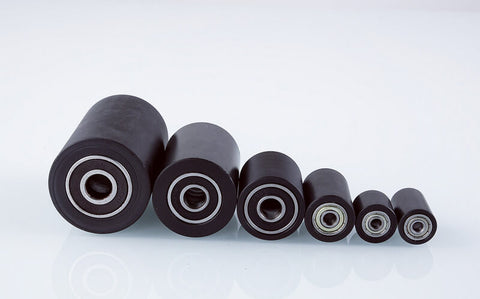
POM vs Nylon in Power Tools
Power tools like drills operate under high torque and temperatures, where POM also has advantages over nylon. One power tool company replaced nylon gears with POM, which reduced wear and friction while improving durability. This translated into tools that could handle more heavy-duty use before needing repair.
POM bushings are another power tool component that see heavy wear. Milwaukee Tools switched from nylon bushings to POM bushings in their latest high-use models, increasing lifespan and reducing noise from friction. The POM parts handled heat generation and load impacts much better compared to nylon.
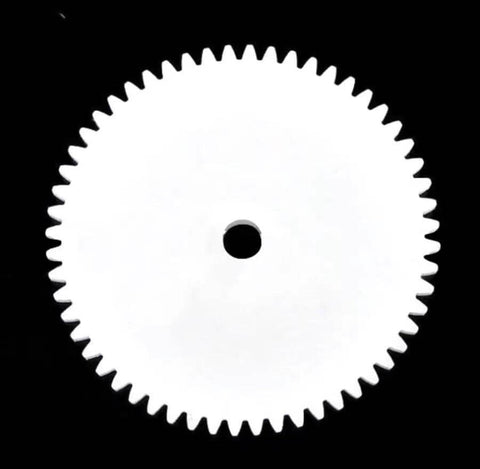
POM vs Nylon in Electronics
Consumer electronics represent another application where POM has started replacing nylon. For example, Sony chosen POM for many components in their latest Playstation 5 controllers, citing both lower costs and easier coloring while retaining strength compared to nylon.
POM's superior electrical insulation properties also make it an alternative to nylon for connectors and other components that require insulation. POM maintains its dielectric properties across a wide temperature range, outperforming nylon.
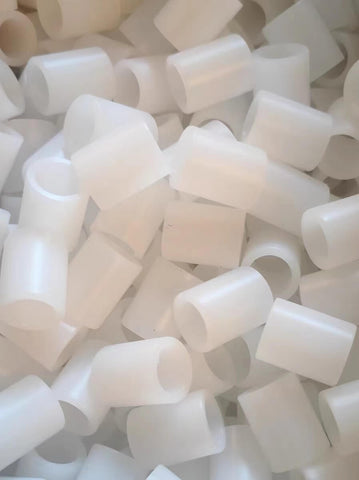
When looking at these real-world examples, we see that POM can outperform nylon in certain high-impact consumer product applications. From food processor blades able to withstand hot water, to humidifier tanks not cracking under humidity, to power tool components lasting longer under high torque, POM demonstrates advantages. Its unique mechanical, chemical, and electrical properties allow it to outlast nylon when factors like heat, chemicals, torque, and humidity are present.
While nylon has been popular for years, the case studies show POM's superior performance under stress. Considering POM as an alternative can result in appliances, power tools, and electronics with improved lifespans. POM's properties translate to consumer products that can handle real-world conditions and avoid failure. When performance matters, these examples make clear that POM can be a better material choice than nylon.
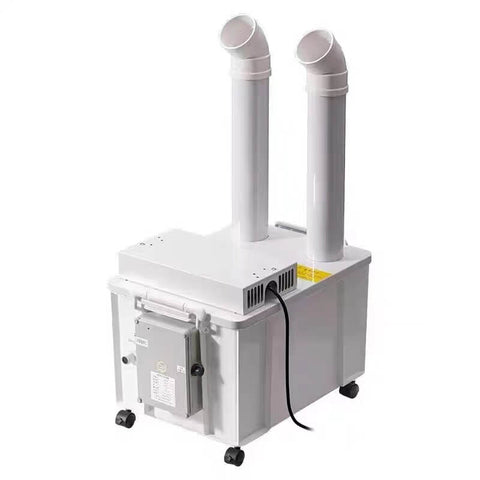