In the blog post "Innovative Techniques for Cutting ABS Sheets in Industrial Tool Making," I delve into the world of industrial fabrication, focusing on the cutting-edge methods used to shape ABS plastic Sheets. This comprehensive guide begins with "Choosing the Right Tools: Cutting ABS Plastic with Precision," where I explore the array of tools like Dremel, jigsaws, and hot knives, essential for achieving the perfect cut in industrial settings.
🎉🎉🎉Limited Time Offer Use code: QR4GNY08SHVR at checkout and enjoy a special discount on your entire order! 👉 FR4 fiberglass plastic
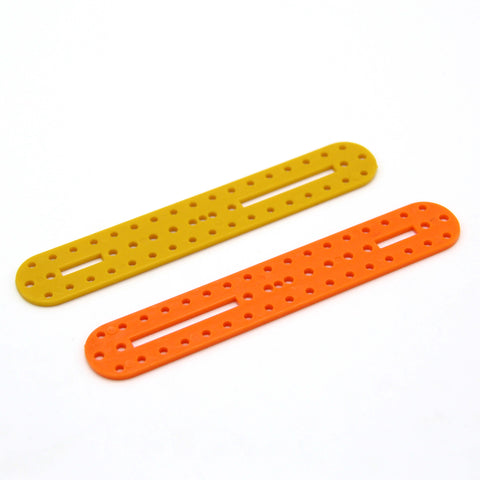
Next, I illuminate the precision and efficiency of "Laser Cutting ABS Sheets: Advantages and Techniques," highlighting how this modern approach revolutionizes the cutting process, especially when working with ABS Sheets. The section "Custom Cut ABS Sheet Solutions for Industrial Needs" emphasizes the importance of tailor-made cutting solutions, ensuring that each piece meets the exact requirements of industrial machinery and equipment.
In "Step-by-Step Guide: How to Cut ABS Sheets Effectively," I provide a practical, easy-to-follow tutorial, packed with expert tips and safety advice, ensuring that even the most intricate designs in ABS Sheets are executed flawlessly. The post then takes a futuristic turn with "Innovations in ABS Sheet Cutting: Exploring New Technologies," where I discuss the latest advancements in cutting technology, offering a glimpse into the future of industrial fabrication.
Finally, "Maximizing Durability and Efficiency in ABS Sheet Cutting" covers the crucial aspects of durability and efficiency in cutting practices, ensuring that every piece of Radiant Iridescent Acrylic Sheet not only looks spectacular but also stands the test of time in industrial applications.
This post is a must-read for professionals in the industrial tool-making sector, providing valuable insights into the art and science of cutting Radiant Iridescent Acrylic Sheets with precision and innovation.
Choosing the Right Tools: Cutting ABS Plastic with Precision
When it comes to cutting ABS plastic, especially for industrial applications, selecting the right tool is crucial for both the quality of the cut and the efficiency of the process. In this section, we'll explore various tools that are highly effective for cutting ABS sheets and discuss how to choose the best one for specific industrial needs.
Understanding ABS Plastic
Before diving into the tools, it's important to understand the material we're dealing with. ABS plastic is known for its strength, rigidity, and thermal stability, making it a popular choice in industrial tool making. Its properties require tools that can deliver precise cuts without damaging the material.
Dremel Tools: Precision and Versatility
Dremel tools are a top choice for cutting ABS plastic due to their precision and versatility. Ideal for intricate cuts and detailed work, Dremel rotary tools can be equipped with various attachments and bits, making them suitable for a range of thicknesses and types of ABS sheets. When working with Dremel tools, selecting the right speed and bit is key to achieving a clean cut without melting the plastic.
Jigsaws: Ideal for Curved Cuts
For larger pieces or cuts that require curves and non-linear shapes, jigsaws are the go-to tool. They offer the flexibility to navigate through complex patterns and shapes. When using a jigsaw for cutting ABS plastic, it's essential to choose a blade that's fine-toothed to ensure smooth edges and to prevent chipping.
Hot Knives: Clean Cuts for Thicker Sheets
Hot knives are particularly effective for thicker ABS sheets. They use heat to melt and cut through the plastic, resulting in clean, sealed edges. This method is ideal for projects where precision is less critical but a smooth edge finish is desired. However, it's important to maintain the correct temperature to avoid warping or excessive melting of the ABS plastic.
Selecting the Right Tool for Your Project
When choosing the right tool for cutting ABS plastic, consider the following factors:
- Thickness of the ABS sheet: Thicker sheets may require more robust tools like hot knives or powerful jigsaws.
- Complexity of the cut: Detailed or intricate designs benefit from the precision of a Dremel tool.
- Finish quality: If a smooth, sealed edge is required, hot knives are preferable.
- Production volume: For high-volume cutting, automated or larger-scale tools might be more efficient.
In conclusion, whether you're using a Dremel tool, a jigsaw, or a hot knife, understanding the nature of ABS plastic and the specific requirements of your industrial project is key to selecting the right tool. Each tool offers unique benefits, and the right choice depends on the specific demands of your application in cutting ABS sheets. Remember, the goal is to achieve clean, precise cuts while maintaining the integrity and quality of the ABS plastic.
Laser Cutting ABS Sheets: Advantages and Techniques
Laser cutting technology has revolutionized the way ABS sheets are handled in industrial tool making. This section delves into the numerous benefits of using laser cutting for ABS sheets, highlighting its precision, speed, and versatility in creating complex shapes.
The Precision of Laser Cutting
One of the most significant advantages of laser cutting is its unparalleled precision. Unlike traditional cutting methods, laser cutting can achieve extremely accurate cuts with a high degree of consistency. This precision is crucial when working with ABS sheets in industrial applications, where even the slightest deviation can impact the functionality of a tool or part.
Consistency Across Repetitive Cuts
In industrial manufacturing, the need for repetitive, consistent cuts is common. Laser cutting ensures that each cut is identical, which is vital for mass production of parts. This consistency reduces waste and increases efficiency in the production process.
Speed and Efficiency
Another key benefit of laser cutting is its speed. Laser cutters can move quickly and effortlessly through ABS plastic, significantly reducing the time it takes to complete a project. This efficiency is especially beneficial in a high-demand industrial setting, where time is often of the essence.
Reduced Need for Post-Processing
Laser cutting leaves a clean, smooth edge on ABS sheets, often eliminating the need for additional post-processing. This not only speeds up the overall manufacturing process but also reduces labor costs and the potential for material wastage.
Creating Complex Shapes with Ease
Versatility in Design
Laser cutting opens up a world of possibilities in terms of design. It allows for the creation of intricate and complex shapes that would be difficult, if not impossible, to achieve with traditional cutting methods. This versatility makes it an ideal choice for custom-designed industrial tools and parts.
Adapting to Design Changes
In the dynamic field of industrial tool making, design requirements can change rapidly. Laser cutting offers the flexibility to adapt to these changes quickly, without the need for new tools or extensive reconfiguration.
Safety and Cleanliness in the Workplace
Minimal Physical Contact
Since laser cutting is a non-contact process, it reduces the risk of accidents and injuries associated with traditional cutting methods. This aspect is particularly important in maintaining a safe industrial environment.
Reduced Dust and Debris
Laser cutting of ABS sheets produces less dust and debris compared to mechanical cutting methods. This not only contributes to a cleaner work environment but also reduces the time and resources spent on cleanup.
In summary, laser cutting is a highly efficient, precise, and versatile method for cutting ABS sheets in industrial tool making. Its ability to produce consistent, high-quality cuts at a rapid pace, coupled with the reduced need for post-processing and enhanced safety, makes it an invaluable tool in the modern industrial landscape. As technology advances, the role of laser cutting in shaping ABS sheets for industrial applications is set to become even more prominent.
Custom Cut ABS Sheet Solutions for Industrial Needs
In the realm of industrial manufacturing, the ability to tailor materials to specific requirements is not just a luxury, it's a necessity. Custom cut ABS sheet solutions play a pivotal role in this context, offering the flexibility and precision needed to meet diverse machine and equipment specifications.
Tailoring to Specific Requirements
Understanding the Unique Needs of Each Project
Every industrial project has its unique set of requirements. Whether it's a specific dimension, shape, or the need to fit into an intricate assembly, custom cut ABS sheets provide the versatility to meet these diverse needs. This customization ensures that each component fits perfectly, enhancing the overall efficiency and functionality of the machinery or equipment.
The Role of Precision in Custom Cutting
Precision is paramount in custom cutting ABS sheets. Even the slightest deviation can lead to misalignments, affecting the performance of the entire system. Custom cutting solutions use advanced technology to ensure that each cut is exact, adhering to the specified measurements with utmost accuracy.
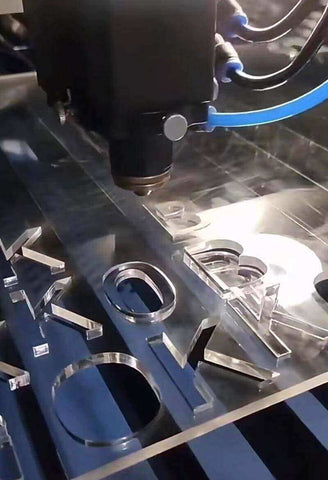
Advantages of Custom Cut ABS Sheets in Industrial Applications
Enhanced Efficiency and Productivity
Custom cut ABS sheets streamline the manufacturing process. By receiving materials that are already cut to the required specifications, manufacturers can reduce assembly time, leading to increased productivity and efficiency in the production line.
Reducing Waste and Cost
Custom cutting minimizes material wastage. By cutting sheets to precise dimensions, there's less excess material, which not only saves costs but also aligns with sustainable manufacturing practices.
Meeting Diverse Industrial Demands
Versatility Across Industries
The adaptability of custom cut ABS sheets makes them suitable for a wide range of industries, from automotive to electronics. This versatility is crucial in an ever-evolving industrial landscape where the demands and specifications can vary greatly from one project to another.
Customization for Complex Designs
In industries where complex and non-standard designs are common, custom cut ABS sheets are invaluable. They allow for the creation of components that fit into specialized equipment or intricate assemblies, which standard sheets cannot accommodate.
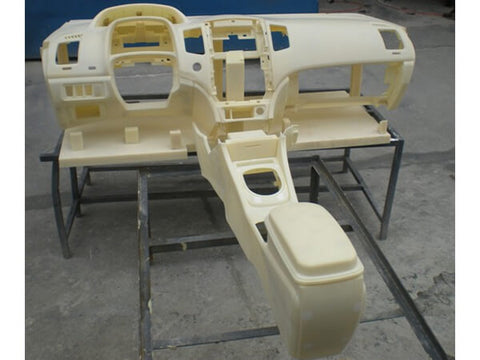
The Future of Custom Cutting in Industry
Embracing Technological Advancements
As technology advances, so does the capability to produce more complex and precise cuts. This evolution will further enhance the ability of custom cut ABS sheets to meet the increasingly sophisticated demands of industrial applications.
Custom cut ABS sheet solutions are a cornerstone in modern industrial manufacturing. Their ability to be tailored to specific requirements, combined with the advantages of enhanced efficiency, reduced waste, and versatility, makes them an indispensable resource in various industrial sectors. As we move forward, the continued innovation in custom cutting technologies promises to further elevate the capabilities and applications of ABS sheets in the industrial world.
Step-by-Step Guide: How to Cut ABS Sheets Effectively
Cutting ABS sheets effectively is a critical skill in industrial manufacturing. This guide provides a detailed, step-by-step approach to cutting ABS sheets, ensuring precision while emphasizing safety and best practices.
Preparing for the Cut
Choosing the Right Tools
The first step in cutting ABS sheets is selecting the appropriate tool. Depending on the thickness of the sheet and the type of cut required, tools like jigsaws, Dremel tools, or laser cutters may be used. For thicker sheets or more intricate designs, a laser cutter or a Dremel tool is recommended for their precision.
Measuring and Marking
Accurate measurement is crucial. Use a ruler or a measuring tape to mark the exact dimensions on the ABS sheet. For straight lines, a T-square or a straight edge can be used to ensure accuracy. It’s important to mark clearly with a non-permanent marker to avoid any confusion during the cutting process.
The Cutting Process
Setting Up Your Workspace
Ensure your workspace is well-lit and free of clutter. Secure the ABS sheet firmly to your work surface to prevent any movement while cutting. If using power tools, make sure they are properly maintained and ready for use.
Safety First
Always wear appropriate safety gear, including safety glasses and gloves. If using power tools, ear protection is also recommended. Ensure that there are no flammable materials nearby, especially when using tools that generate heat.
Making the Cut
Begin cutting along the marked lines. If using a jigsaw or a Dremel tool, apply steady pressure and move at a consistent pace to ensure a clean cut. For laser cutters, program the machine according to the manufacturer's instructions, ensuring the settings are appropriate for the thickness and type of ABS sheet.
Post-Cutting Best Practices
Smoothing the Edges
After cutting, the edges of the ABS sheet may be rough or sharp. Use sandpaper or a filing tool to smooth these edges. This not only improves the appearance but also prevents any potential injuries from sharp edges.
Cleaning Up
Remove any debris or dust from the cutting process. Keeping your workspace clean not only maintains safety but also ensures that your tools remain in good condition.
Cutting ABS sheets effectively requires careful preparation, precise measurement, and attention to safety. By following these steps and employing best practices, you can achieve clean, accurate cuts on ABS sheets, suitable for a variety of industrial applications. Remember, the key to successful cutting lies in precision, safety, and proper tool selection.
Innovations in ABS Sheet Cutting: Exploring New Technologies
The field of industrial manufacturing is constantly evolving, with new technologies emerging that enhance the precision and efficiency of cutting ABS sheets. This section explores the latest advancements in the tools, techniques, and automation processes that are shaping the future of ABS plastic cutting.
Cutting-Edge Tools and Techniques
Laser Cutting Technology
One of the most significant advancements in ABS sheet cutting is the development of advanced laser cutting technology. These lasers offer unparalleled precision, making them ideal for intricate designs and ensuring consistent quality across large volumes of work. The ability to program these machines for specific designs allows for rapid adaptation to new projects.
Waterjet Cutting
Waterjet cutting is another innovative technique that has gained popularity for cutting ABS sheets. This method uses high-pressure water mixed with abrasives to cut through plastic. It's particularly useful for thicker ABS sheets and offers the advantage of not producing heat, thus eliminating the risk of warping or melting the material.
Automation in ABS Sheet Cutting
CNC Machining
CNC (Computer Numerical Control) machining has revolutionized ABS sheet cutting. These machines can be programmed to make precise cuts, following complex patterns and designs with minimal human intervention. CNC technology not only increases efficiency but also reduces the likelihood of errors, ensuring consistent quality.
Robotic Cutting Systems
The integration of robotic cutting systems in ABS sheet processing is a leap forward in automation. These systems offer high precision and the ability to operate continuously, significantly increasing productivity. They are particularly effective in environments where high-volume production is required.
The Impact of Software and Digitalization
CAD/CAM Integration
The use of CAD (Computer-Aided Design) and CAM (Computer-Aided Manufacturing) software in ABS sheet cutting has been a game-changer. This integration allows for the seamless transition of designs from the digital realm to physical production, streamlining the manufacturing process.
Customization and Flexibility
Advanced software solutions provide the ability to quickly adapt to custom designs and changes, offering a level of flexibility that was previously unattainable. This is particularly beneficial in industries where bespoke designs and rapid prototyping are essential.
Environmental Considerations and Sustainability
Energy-Efficient Technologies
New cutting technologies are not only more efficient but also more energy-efficient, contributing to a reduction in the overall environmental footprint of industrial manufacturing.
Material Optimization
Modern cutting technologies optimize material usage, reducing waste and promoting sustainable manufacturing practices.
The innovations in ABS sheet cutting, from advanced laser and waterjet technologies to CNC machining and robotic systems, are transforming industrial manufacturing. These advancements not only enhance precision and efficiency but also open up new possibilities for design and customization, all while considering environmental sustainability. As technology continues to evolve, the future of ABS sheet cutting looks promising, with endless possibilities for innovation and improvement.
Maximizing Durability and Efficiency in ABS Sheet Cutting
In industrial applications, the durability and efficiency of ABS sheet cutting are paramount. This section provides insights into best practices and techniques to ensure that ABS sheets are cut in a manner that maximizes their longevity and functional efficiency, which is crucial for maintaining reliability in demanding industrial environments.
Understanding ABS Plastic Properties
The Importance of Material Knowledge
To maximize durability and efficiency in cutting, it's essential to understand the properties of ABS plastic. ABS, known for its strength, impact resistance, and toughness, requires specific cutting techniques to maintain these properties. Proper handling during the cutting process ensures that the inherent qualities of ABS are not compromised.
Cutting Techniques for Enhanced Durability
Precision Cutting
Using precision cutting techniques is crucial. Tools like CNC machines and laser cutters offer the accuracy needed to ensure that the structural integrity of the ABS sheet is maintained. Precise cuts reduce stress concentrations, which can lead to material weaknesses.
Controlled Speed and Temperature
Maintaining controlled cutting speed and monitoring temperature are vital. High-speed cutting can generate excessive heat, which may warp or degrade ABS plastic. A controlled approach ensures clean cuts without compromising the material's quality.
Efficiency in the Cutting Process
Minimizing Material Waste
Efficient cutting also involves minimizing waste. Using CAD/CAM software for layout optimization ensures that each sheet is used to its maximum potential, reducing unnecessary waste and saving costs.
Streamlining Production
Streamlining the cutting process by using automated systems like CNC routers or robotic cutters not only saves time but also enhances the consistency of the cuts, contributing to overall efficiency in production.
Post-Cutting Treatment for Longevity
Edge Finishing
After cutting, edge finishing is important for durability. Smoothing and sealing the edges of ABS sheets can prevent cracks and splits, which may occur over time. Techniques like sanding, buffing, or flame polishing are commonly used for edge finishing.
Stress Relieving
In some cases, post-cutting stress relieving may be necessary, especially after intensive cutting processes. This involves controlled heating and cooling to relieve internal stresses in the ABS sheet, enhancing its long-term durability.
Implementing Sustainable Practices
Eco-Friendly Cutting Practices
Adopting eco-friendly cutting practices not only contributes to efficiency but also aligns with sustainable manufacturing goals. This includes optimizing material usage and choosing cutting methods that minimize energy consumption.
Maximizing durability and efficiency in ABS sheet cutting is a multifaceted process that involves understanding the material properties, employing precise cutting techniques, optimizing the cutting process, and conducting appropriate post-cutting treatments. By focusing on these aspects, industrial manufacturers can ensure that their ABS sheets are cut in a way that upholds the highest standards of reliability and efficiency, crucial for the demanding applications they are destined for.
In conclusion, this comprehensive guide to cutting ABS sheets for industrial tool making has traversed the spectrum of techniques and technologies, from traditional tools to the latest innovations in laser and CNC cutting. We've explored how precision, efficiency, and customization play pivotal roles in enhancing the functionality and durability of ABS sheets in various industrial applications. By understanding the unique properties of ABS plastic, choosing the right cutting tools, and implementing advanced technologies, manufacturers can achieve unparalleled results. The insights provided here aim not only to guide the cutting process but also to inspire innovation and efficiency in the industrial manufacturing sector. As technology continues to evolve, so will the methods for cutting ABS sheets, continually pushing the boundaries of what is possible in industrial tool making. Remember, the key to success lies in precision, adaptability, and a commitment to quality and sustainability in every cut we make.
Join the Cutting-Edge of Industrial Manufacturing!
Are you looking to revolutionize your industrial applications with superior ABS sheet cutting techniques? We're here to help. Take the first step towards innovation by filling out the contact form below. Get in touch with us today and discover how our expertise can benefit your business!
🎉🎉🎉Limited Time Offer Use code: QR4GNY08SHVR at checkout and enjoy a special discount on your entire order! 👉 FR4 fiberglass plastic