When it comes to industrial parts processing, few materials offer the versatility and performance of ultra-high molecular weight (UHMW) polyethylene sheets. As a unique class of high-performance polymers, these durable industrial plastics enable unmatched capabilities enhancing productivity, longevity and quality.
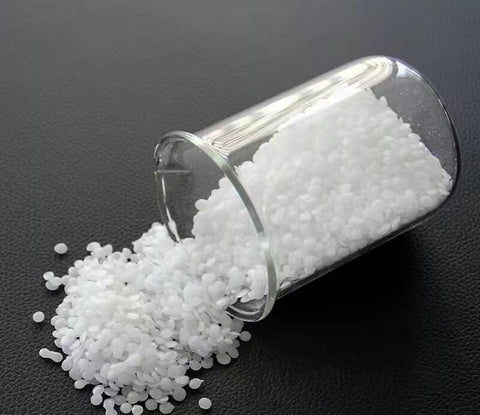
Introduction to UHMW Sheets: Understanding the Basics
UHMW sheets refer to thermoplastic polyethylene materials composed of extremely long molecular chains, delivering exceptional properties like:
- Peerless strength and rigidity
- Unrivaled abrasion and chemical resistance
- Low-friction and self-lubricating surfaces
Their superiority stems from molecular chains spanning over 6 million molecular weight - compared to just 50,000 in regular polyethylene.
Key Properties of UHMW Sheets in Parts Processing
The molecular structure of UHMW lends exceptional performance properties that directly benefit parts processing:
Extreme Abrasion Resistance
With hardness valued on the R scale at 60-68, UHMW demonstrates upto 30 times longer wear life over general plastics like HDPE, nylon and acetal. This resistance to abrasive friction aids consistent output.
Resilient Impact Strength
Exceptional tensile strength above 35 MPa allows UHMW sheets to endure application demands like pressing, stamping and hammering without cracking or crimping. High flexibility maintains integrity despite compression, shocks and vibration.
Inherent Lubricity
The slick, waxy surface structure functionally eliminates stick-slip while moving along metal or plastic. This allows smooth, low-friction motion critical for fabrication processes and preventing jamming.
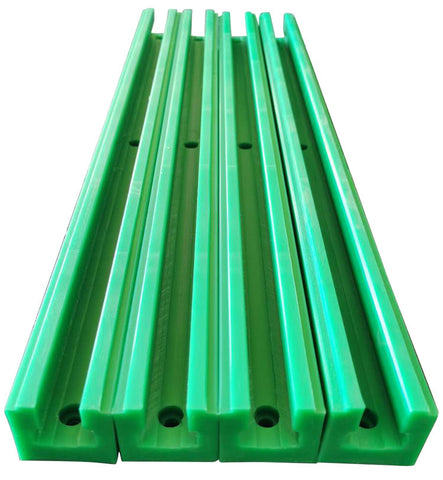
Comparing UHMW Sheets with Other Industrial Materials
Bench-marked against other core plastics and metals used in parts manufacturing, UHMW polyethylene sheets demonstrate outright advantages:
Versus HDPE
Standard high density polyethylene offers reasonable strength but lacks abrasion resistance for demanding processes. It also has poorer self-lubrication, requiring external lubricants. UHMW outclasses HDPE 2-fold in key aspects:
- Tensile strength
- Hardness
- Thermal stability
Versus Acetal
Engineering polymer acetal resins (POM) provide stiffness and precision properties. However, their capacity to handle repetitive stress is inferior to UHMw. For maintaining precision despite heavy loads, UHMW bears 3 times longer lifespan over acetal.
Versus Nylon
While more heat-resistant than polyethylene, nylon suffers from moisture absorption issues. This results in dimensional instability and fouling in wet environments - demanding exclusion for food contact zones. UHMW conversely avoids moisture issues, retaining stable properties.
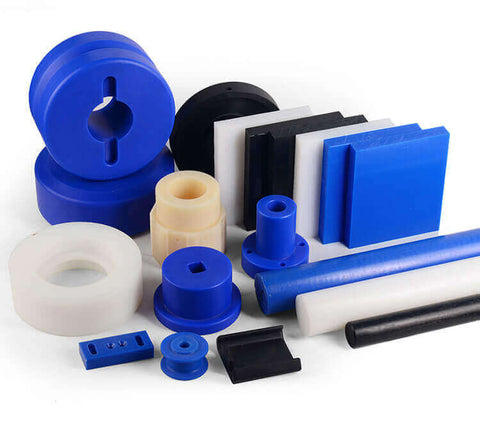
Innovative Applications of UHMW Sheets in Parts Manufacturing
Owing to the well-rounded properties suiting countless demands, UHMW allows breakthrough applications across machining and fabrication:
Molds and Tooling
Leveraging the slick, non-stick surface while withstanding high tonnage, UHMW lines injection molds and tooling - optimizing flow and release while minimizing wear. Being food-compliant, it serves ingeniously for chocolate and biscuit molding.
Chute Linings
Subjected to sliding abrasion from aggregates, metals and chemicals, UHMW sheets line industrial hoppers, bunkers and chutes - standing up to punishment while allowing complete material discharge. Its low-friction surface drastically improves flow rates.
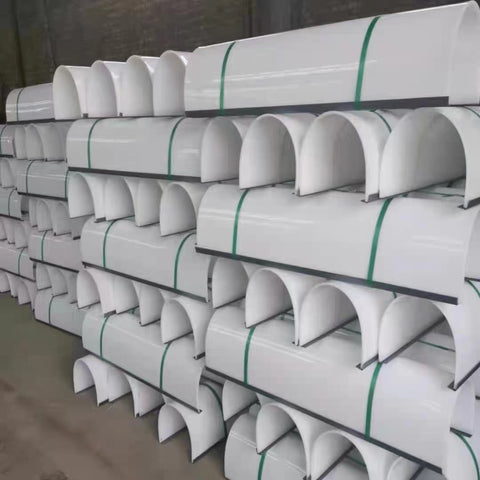
Cleanroom Equipment
With high chemical resistance and non-particulating surface, UHMW suits extremely well for institutional cleanroom equipment. This includes wafer transport carriers in semicon factories, lab sample couriers and IV bag making machinery.
Customizing UHMW Sheets for Specific Parts Processing Needs
Beyond off-the-shelf forms, UHMW can be customized via:
Dimensional Fabrication
Offering CAD-based fabrication, sheet dimensions can be precision-cut in exact lengths, widths and shapes to fit unique component dimensions. This reduces scrap generation.
Thickness Variants
From tiny 1/32 inch films to massive 4 inch plates, varying thickness suits specific application demands like load-bearing capacity. Thinner types work for slides and glides while thick variants endure high tonnage.
Performance Tailoring
Introducing custom additives like PTFE or molybdenum disulfide into the UHMW base further enhances traits like lubrication, conductivity and static control as required per application settings.

Case Studies: Success Stories with UHMW Sheets in Parts Processing
Across production environments, UHMW unlocks immense value:
Automotive Stamping
Leading truck body panel maker Trailmobile Products uses 3⁄8 inch thick UHMW sheets to line high tonnage stamping plates. Despite enduring 400 tons of pressure with minimal lubrication, UHMW liners last over 5 years - outperforming other materials.
Meat Processing Conveyors
Meat maven Maple Lodge Farms leverages 1⁄4 inch thick UHMW sheets to modify existing stainless steel conveyor belt guides. Keeping the FDA-approved UHMW lining along the metal contact face seamlessly avoids jamming issues while complying with stringent sanitation needs.
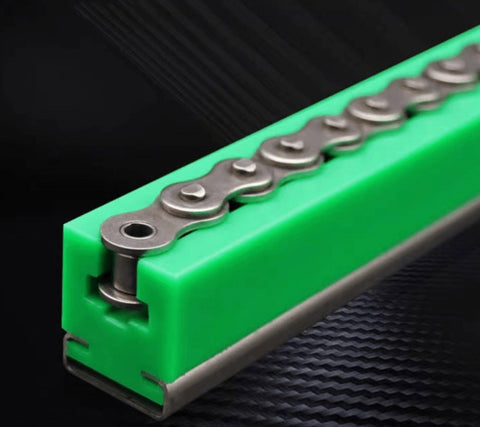
Maintaining and Handling UHMW Sheets for Longevity
To sustain high performance, adopting best practices around UHMW proves critical:
Storage Protocols
Always rest sheets on flat, dry racks away from sunlight and harsh lighting. Warping from improper storage can degrade strength. Use spacing elements to prevent permanent deformation from load pressures when stacking.
Cleaning Methods
General soap and water washing suffices most cleaning needs. Avoid using heat, solvents or harsh abrasives which can erode surfaces. Mechanical inline brush washers also work well for heavier contaminant removal while protecting sheet integrity.
Cost-Benefit Analysis of Using UHMW Sheets in Production
Weighing total cost of ownership reveals UHMW’s immense value:
Enduring Lifespan
A lifespan 5-10 times longer over regular plastics and metals signifies lower replacement costs - saving future purchase and machining expenses.
Operational Efficiency
Superlative abrasion resistance ensures reliable, failure-free performance. This translates into production continuity and capacity utilization.
Quality Output
Exceptional strength properties also enable flawless, consistent parts processing - ensuring high-grade end products and minimum rejects.
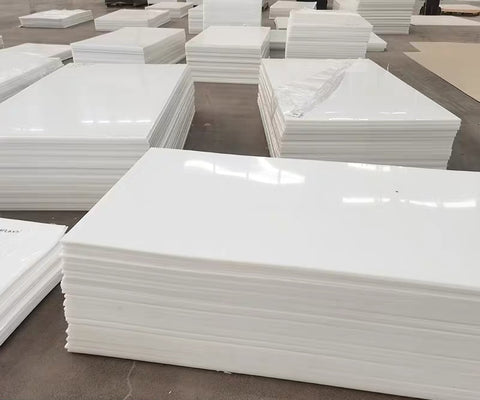
Future Trends: UHMW Sheets in Emerging Technologies
Ongoing innovation promises exciting new potentials:
Hybrid Advancements
Reinforcing UHMW with nanoparticles like graphene for customized composites shows early promise - already demonstrating up to 10 times improvement in strength in labs. Development of such hybrids can stretch capabilities.
Smart UHMW Sheets
Early research in integrating thin-film sensors within UHMW aims to enable real-time diagnostics for identifying microscopic damage before catastrophic failure. The smart UHMW sheets seek to enhance predictive maintenance.
Why UHMW Sheets Are Essential for Modern Parts Processing
Given the unmatched durability, customization agility, processing ease and sustainability benefits, UHMW polyethylene sheets deliver invaluable versatility enabling quality and productivity enhancement across machining and fabrication applications in automation, aerospace, semiconductors and medical equipment sectors.