Bakelite, the world's first fully synthetic plastic, marked a revolution in materials science when it was invented in 1907 by Belgian-American chemist Dr. Leo Baekeland. With its unique properties, versatility, and affordability, Bakelite was soon mass-produced and widely used in everything from electronics to jewelry to cookware. Though later eclipsed by other modern plastics, Bakelite still holds an important place in the history of industrial design and continues to attract collectors today.
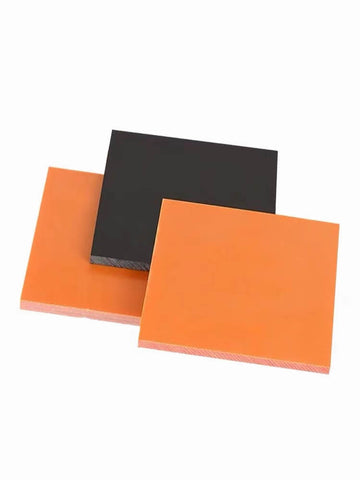
A Revolutionary Invention by Dr. Leo Baekeland
The creation of the first fully synthetic plastic all started with Leo Baekeland's quest to find a replacement for shellac, a resin secreted by the female lac bug. Shellac had become increasingly expensive due to supply shortages, yet it was an essential material used for insulation in the booming electrical industry in the early 1900s.
As a chemist experimenting in his home laboratory in Yonkers, New York, Leo Baekeland began combining phenol and formaldehyde under heat and pressure to produce a hard, molded material that could effectively replace shellac as an electrical insulator. After years of adjustments and refinements, Baekeland filed a patent for this pioneering “heat-resistant plastic” in 1907 and named his invention Bakelite. The patent outlined methods for the production of Bakelite that created strong, infusible, and insoluble materials made from phenol and formaldehyde.
Baekeland continued to refine Bakelite's chemical formula, process, and applications. By 1909, the promising new material was unveiled to the public. The Belgian-born “Father of Bakelite” dutifully promoted his invention at the meeting of the American Chemical Society on February 5, 1909. There he described the history, technical details, and possibilities of Bakelite.
Baekeland boldly declared: “"The immediate future will see the use of Bakelite in various forms for electrical insulators, switch bases, lab wares, and other applications.” His predictions proved prescient. By 1912, Bakelite was in wide use for industrial applications across America and Europe.
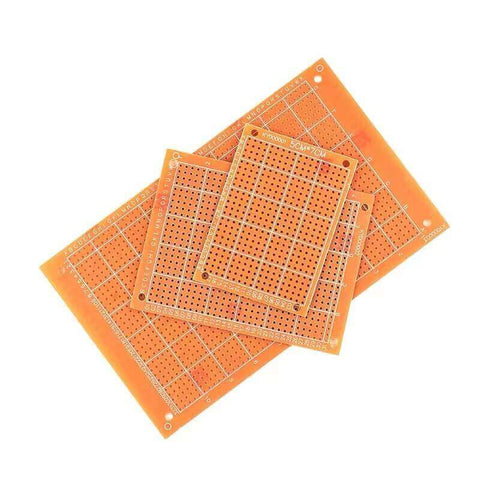
The Versatile Properties of Bakelite Make It Ideal for Mass Production
What set Bakelite apart from previous plastics was that it was truly the first synthetic plastic resin that could be completely molded while heated and retain its shape when cooled. Natural plastics like cellulose nitrate can be molded but are limited by their low melting points. In contrast, Bakelite offered high heat resistance and thermosetting properties that allowed it to be shaped into permanent, durable forms.
Some of the unique properties that contributed to Bakelite's versatility as a molding plastic included:
- Electrical insulation - As an electrical insulator, Bakelite made an optimal replacement for shellac. It resisted the flow of electrical current, provided protection from electrical shock, and insulated wiring.
- Heat and flame resistance - Bakelite was resistant to heat and flames up to 350°C/ 662°F before charring would occur. This allowed it to be used for hot household appliances.
- Low moisture absorption - Bakelite repelled water and moisture, which made it suitable for marine and bathroom applications.
- Chemical resistance - Insoluble in alcohol, weak acids and bases, Bakelite was impervious to deterioration from common solvents.
- Mechanical strength - Moldings had high strength and stiffness along with resistance to chipping and cracking.
- Dimensional stability - Bakelite resists warping from exposure to heat, cold, or water over time. This stability and durability contributed to Bakelite's long service life.
These characteristics enabled Bakelite to be both molded precisely into unlimited shapes, sizes, and colors while retaining exceptional structural integrity and longevity.
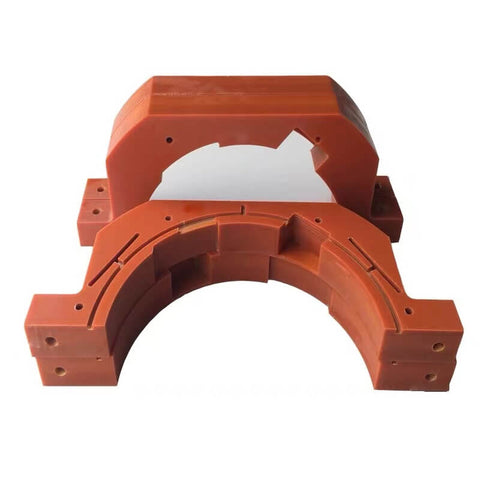
Bakelite Ushered in an Era of Plastics in the Early 1900s
The invention of Bakelite occurred just as revolutionary breakthroughs in synthetic materials like celluloid and rayon were galvanizing the plastics industry. Bakelite served as a key driver in the expansion of molded plastics by demonstrating the vast new potential of these materials for mass production and commercial use.
The Bakelite Corporation was formed in 1910, and the first Bakelite factory opened in Bound Brook, New Jersey in 1911. By 1912, designer and innovator Marcel Schmuziger had patented a technique to streamline the production of molded Bakelite products like billiard balls, poker chips, and varnish. Bakelite’s affordability and malleability soon made it ubiquitous.
As production scaled up to meet soaring demand, Bakelite was used for everything from electrical gadgets and automobile parts to cameras, costume jewelry, and even kitchenware. It was also famously used in patriotic applications during World War I and World War II, such as gas masks and helmet linings.
Vintage Bakelite radios first emerged in the 1920s and took on colorful, stylized designs with Catalin and Prystal models leading the market. Bakelite kitchen tools like egg beaters and hourglass egg timers also became popular during this era.
By the 1930s Art Deco period, Bakelite jewelry had come into vogue. Dramatic bangles, rings, earrings, and brooches showcased the smooth, polished patina and rich colors possible with molded Bakelite. Iconic designers like Coco Chanel began incorporating Bakelite into their avant-garde jewelry collections.
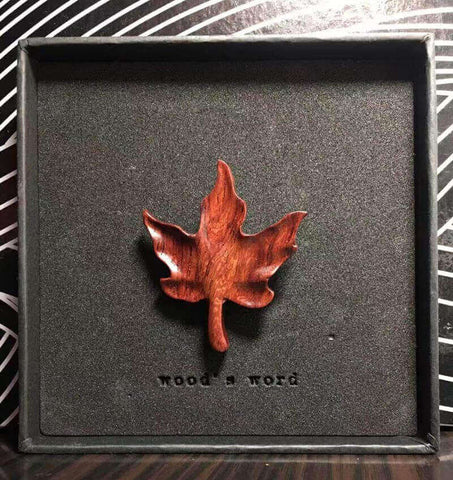
Key Characteristics That Made Bakelite a Go-To Industrial Plastic
During the interwar period of the 1920s to 1940s, Bakelite enjoyed immense commercial success and became embedded in everyday life. The world marveled at this wondrous new plastic material. So what exactly triggered the Bakelite sensation and made it the must-have plastic of its time?
Affordability - Bakelite could be produced very cheaply by molding a mixture of phenol from coal tar and formaldehyde under heat and pressure into a thermosetting resin. These inexpensive base ingredients made Bakelite products very affordable compared to other materials.
Versatility - As discussed earlier, Bakelite’s unique properties enabled it to be molded into practically any shape while retaining its structural integrity. This versatility opened up new horizons for plastic product design.
Ease of Application -Bakelite is lightweight, easy to machine into products and resistant to deformation, making it easy to incorporate into existing product designs. It provides the impetus for rapid prototyping and innovation.
Color and Finish - Pigments could be mixed into the resin to produce vivid colors like "apple juice" red and butterscotch. The smooth polished patina gave Bakelite an attractively glossy finish.
Strength and Durability - Bakelite’s high mechanical strength and resistance to heat, water, and chemicals gave it unrivaled longevity and performance over traditional materials like rubber or celluloid.
Electrical Insulation - With its electrical resistance, Bakelite elegantly solved the problem of dangerous shorts and fires in the thriving electronics industry.
These winning characteristics solidified Bakelite as a preferred industrial plastic across diverse manufacturing sectors. Bakelite fueled modern product design and allowed plastic to emerge as an essential general-purpose material.
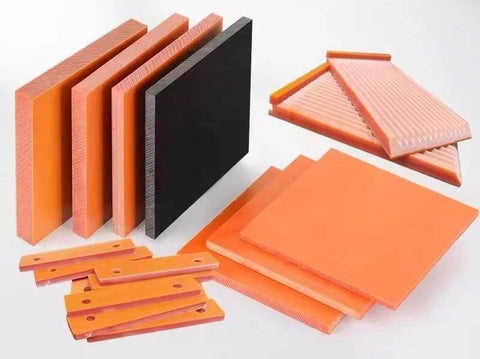
The Decline of Bakelite in the Mid-20th Century
By the early 1940s, Bakelite accounted for thousands of daily use items, from telephones to toys. Over 5,000 US patents referenced Bakelite or featured Bakelite components. However, around this time, the plastic began losing ground to new synthetic polymers engineered to surpass Bakelite’s limitations.
Competitor plastics gradually chipped away at Bakelite’s market share:
- Nylon (1930s) - Stronger, more flexible, with higher heat resistance
- Polystyrene (1930s) - Cheaper and easier to mold than Bakelite
- Polyethylene (1940s) - More chemically inert and flexible than Bakelite
- PVC (1940s) - Tough and long-lasting; replaced Bakelite in wiring
These new plastics could be specifically formulated for designated purposes where Bakelite fell short. Combined with supply constraints during World War II, Bakelite was dealt a declining role in manufacturing by the 1950s.
Usage of Bakelite dramatically decreased further with the proliferance of high-tech thermoplastics like polycarbonate in the 1960s and 70s. These left thermosetting Bakelite behind.
The Collectible Allure of Vintage Bakelite
Though Bakelite became obsolete and was replaced by more advanced modern plastics, vintage Bakelite products from the 1920s-40s era continue to be sought-after collector’s items. The artistry, glamour, and nostalgia of old Bakelite radios, jewelry, and housewares fuels a thriving market of Bakelite aficionados.
Key drivers of the enduring appeal of vintage Bakelite include:
- Distinct Material Qualities - The look and luster of aged Bakelite cannot be perfectly replicated. Collectors appreciate its unique patina.
- Handcrafted Artistry - Each vintage Bakelite piece carries the fingerprints of dedicated designers and craftspeople. Their artistry is treasured.
- ** Historic Significance** - Bakelite represents a milestone in materials history and industrial design evolution. It has special historical import.
- Nostalgic Design - The Art Deco and mid-century modern aesthetic of Bakelite products trigger fond memories and feelings.
On sites like Etsy and eBay, authentic vintage Bakelite continues to command high prices from avid collectors. Bakelite’s legacy lives on thanks to those who value its origins.
Bakelite's Pivotal Role in the Plastics Revolution
In spite of its gradual decline in favor of more advanced polymers, Bakelite still occupies an unforgettable place in the annals of plastics history. The invention of Bakelite marked a turning point by demonstrating the enormous potential of chemically engineered plastics to transform manufacturing and product design for the better.
Thanks to Dr. Leo Baekeland's pioneering Bakelite research, the world saw plastics evolve from cheap substitutes to versatile high-performance materials offering endless possibilities. Bakelite paved the way for the plastics booms of the mid-late 20th century. It remains appreciated as a groundbreaking innovation both technologically and stylistically.
While Bakelite itself may no longer be a dominant plastic, it still continues to influence modern product manufacturing as well as industrial design. Bakelite's legacy persists in its role establishing plastics as essential synthetic materials for building our fabricated future.
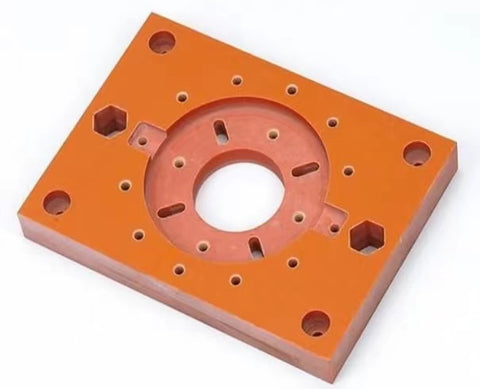