In today's competitive manufacturing landscape, choosing the right materials is crucial in determining the success of a product. ABS plastic has emerged as a versatile and reliable option for designers and engineers across industries. This article provides a comprehensive guide to designing custom ABS parts that are optimized for durability, functionality, and aesthetics.

Understanding ABS Plastic Properties and Manufacturing Processes
ABS (Acrylonitrile Butadiene Styrene) is a common thermoplastic polymer revered for its strength, rigidity, and resistance to physical impacts. It has a glossy appearance and can be injection molded into complex and intricate shapes. ABS plastic strikes the perfect balance between sturdiness and ductility.
Here are some key properties and advantages of ABS plastic:
- High impact resistance - Its rubber-like properties allow it to withstand bumps, drops, and rough handling.
- Dimensional stability - Maintains shape even under fluctuating temperatures.
- Easy machinability - Can be sawn, drilled, filed, and lathed easily.
- Good thermal insulation - Low thermal conductivity makes it suitable for appliances.
- UV radiation resistance - Formulated grades offer protection against sunlight damage.
- Electrical insulation - Does not conduct electricity, making it perfect for electronics.
- Chemical resistance - Unaffected by dilute acids, alkalis, and oils.
- Aesthetic appeal - Glossy finish and ability to be color pigmented.
ABS plastic can be shaped into products using processes like:
- Injection molding - For high volume production of intricate plastic parts.
- 3D printing - For rapid prototyping and low volume production.
- Thermoforming - For making plastic sheets into diverse shapes.
- Extrusion - For long plastic profiles like pipes and tubes.
- Machining - For drilling, milling and other subtractive processes.

Step-by-Step Guide to Designing Custom ABS Parts
Designing functional and robust ABS plastic parts requires technical expertise along with creativity. Follow these steps:
Conceptualization
Start with a clear design brief - consider the purpose of the component, operating conditions, target users, size constraints, etc. Market research and brainstorming can help develop the concept.
Modeling
Use CAD software to create 3D models and 2D technical drawings. Perform simulation tests to visualize mechanical stresses and thermal flows. ABS plastic grades can be selected based on performance requirements.
Prototyping
3D print or machine prototypes to verify fit, form, and functionality before mass production. Build in allowances for ABS plastic shrinkage during molding. Test prototypes rigorously under expected operating conditions.
Tooling
Design and machine injection molds, jigs, fixtures based on prototypes. Use CNC machining for making molds with tighter tolerances for dimensionally accurate ABS parts.
Part Production
Select a suitable ABS plastic molding process and certified plastic manufacturer. Injection molding is ideal for complex and high-precision parts in large volumes. Set molding parameters like temperature, pressure, etc. appropriately.
Post-Processing
Carry out additional finishing processes like deburring, smoothing, painting, pad printing, electroplating, etc. ABS plastic welding and adhesive bonding can help join assemblies.
Quality Testing
Rigorously test final ABS parts under real-world operating conditions. Analyze the effects of temperature, UV, chemicals, wear and tear. Improve designs based on failure data.

Best Practices for Designing Durable ABS Plastic Parts
Follow these vital design guidelines to develop ABS parts that last:
- Maintain uniform wall thickness throughout the part for even cooling and minimum ABS plastic warpage.
- Incorporate generous fillets and radii instead of sharp corners to distribute stress over larger areas.
- Use ribs and gussets around mounting bosses and high load areas to reinforce weak sections prone to failure.
- Follow recommended ABS plastic welding techniques like using compatible solvent cement or vibration welding when joining parts.
- For parts with intricate details and tolerance requirements, opt for CNC machined ABS plastic instead of 3D printed prototypes and molds.
- Avoid using ABS where solvents like acetone are present as it can cause cracking - consider more chemical-resistant materials like polycarbonates or nylons instead.
- For outdoor applications, use UV-resistant ABS grades or coatings that protect against sunlight degradation.

Challenges in Working with ABS Plastic
Despite its popularity, ABS comes with the following design and manufacturing challenges:
Thermal Management
ABS plastic forming processes involve heating the material to high temperatures, making cooling and temperature control paramount. Insufficient cooling causes warping.
Bonding Difficulties
Joining ABS parts through adhesives, welding, fasteners can be problematic and needs extensive trial-and-error. Mating surface preparation is critical.
Limited Chemical Resistance
ABS offers low resistance to concentrated acids, ketones, esters and several other chemicals, limiting suitable applications.
Secondary Finishing
ABS can be difficult to paint or plate uniformly due to its slippery surface. Usually requires specialized surface treatment.
Environmental Factors
ABS is non-biodegradable and harder to recycle compared to metals and glass. Needs thoughtful end-of-life planning.

Expert Tips for Maximizing ABS Plastic Part Longevity
Follow these pro tips to ensure your custom ABS plastic parts enjoy a long service life:
- Select the highest grade ABS plastic from leading manufacturers for best durability. Avoid subpar recycled resins.
- For color requirements, use pre-pigmented ABS instead of painting to prevent coating damage, chips and fading.
- Consider press-fitting, tabs, snap-fits instead of threads or adhesives for simple and fail-proof assembly.
- Incorporate stainless steel or brass inserts with heat resistance for securely fastening ABS parts subjected to frequent loading.
- Analyze heat flow and coolant channel placement when ABS plastic molding to prevent uneven cooling and warping.
- Use ULTEM, PEEK, or polycarbonate molds for longest life when injection molding with corrosive high-temperature ABS.
- Store ABS parts away from sources of heat, sunlight, harsh chemicals and mechanical damage.
With growing demand for visually appealing yet tough products across industries, ABS plastic has established itself as a versatile design staple. By adopting its strengths and catering to its limitations from the initial concept stages, engineers can develop ABS parts that deliver optimized functionality, safety and life expectancy. Leveraging emerging technologies like additive manufacturing and CNC machining while adhering to fundamental design principles will unlock the full potential of ABS plastic.
Let us know your biggest challenges and successes in designing ABS components! Our experts are eager to provide insights and recommendations to help you maximize plastic product durability.
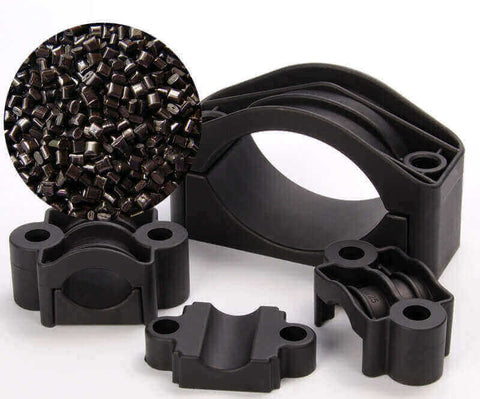